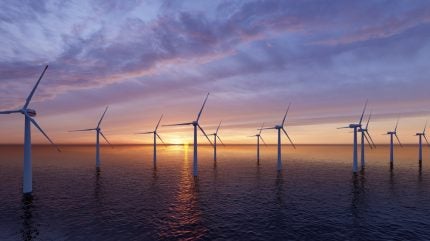
Technological advances in wind-turbine design have made an impressive contribution to the efficiency of wind energy production while lowering the operational costs. Combined with global initiatives and environmental commitments, wind power is now a more viable and competitive renewable energy source. Still, despite this progress, some challenges remain.
Over the past 10 years, the growth of wind power has seen a significant increase across various regions globally and is set to continue. According to analysis from GlobalData, China’s cumulative installed capacity by 2030 is expected to reach 800 GW whilst the US wind energy industry is projected to increase its cumulative installed capacity to 191.1 GW in 2027. Within the EU, the European Commission has ambitious plans to boost the European wind power industry as part of the strategy that 42.5% of EU energy is from renewable resources by 2030.
As technological advancements in design have increased turbine efficiency, there remain operational and maintenance challenges within the turbine system itself. Addressing these challenges proactively can have a strong impact on the wind power industry’s potential moving forward.
Hydraulic systems remain a key component to the workings of wind turbines. Turbines are constantly exposed to the elements – wind, salt, sand, windborne debris and moisture. All of which can cause the breakdown of the hydraulic systems, triggering operational failure, which shortens the equipment’s lifespan, reduces energy generation, and increases the frequency of repairs. Protecting these systems on the front end is vital to increasing turbine productivity over the long term.
Preventative maintenance is key
Leigh Carlson, chief executive officer of US-based Fluid Control Services, who has been supplying wind energy manufacturers a product called the Seal Saver that is designed to protect their hydraulic cylinders, highlights the growing importance of preventative maintenance in offshore wind turbines: “Wind technology is an expanding industry, and maintaining the efficiency of these turbines is key to meeting energy demands.”
Most on and offshore turbines are especially difficult and costly to repair due to both turbine design and remote wind farm locations. This makes preventative maintenance even more critical in wind energy operations. A simple, preventative measure to increase the longevity of hydraulics and reduce downtime is the use of hydraulic guards to protect cylinders.
“Hydraulic cylinders play a crucial role in the wind energy sector as they control the pitch of the wind turbine blades. However, wind turbines, by their nature, are exposed to the elements. The Seal Saver shields hydraulic cylinders from these hazards, extending the life of the equipment, reducing downtime, and saving companies significant repair costs,” says Carlson.
The Seal Saver is a deceptively simple, yet unique, solution – a completely custom-fitted protective cylinder boot, made in a range of durable materials, designed to shield hydraulic cylinders from the harsh environments that turbines are working in. The Seal Saver has a decades long proven track record of protecting cylinder seals and rods on wind turbine machinery against premature failure. Installation is straightforward and usually takes less than 15 minutes. The cylinder does not need to be disassembled, and the only tool needed is a screwdriver.
In comparison to other protective solutions which require machine downtime and extensive labour to install, Seal Saver stands out for its ease of use. An added benefit of this feature is that allows operators to integrate the product into their regular maintenance routines without disrupting operations.
Making headway but operational concerns still need to be considered
As the wind technology industry continues to improve and innovate their turbines to increase productivity, it is important that measures are also taken to reduce the occurrence of hydraulic systems failure. The most successful companies will understand that preventative maintenance should be one of the key considerations to address when operating a wind turbine to ensure their turbines run as efficiently as possible over their lifespan, which will have an impact on their bottom lines. Adding the Seal Saver into the equation is a simple, cost-effective tool that not only will provide companies with a strong ROI but also will aid in creating a better safety culture by protecting the hydraulic system that is running the turbines and decreasing on-site repairs.