Booming EV Sales Challenge Mineral Supply Chains
The global electric car fleet is expanding rapidly. While Tesla still dominates the electric vehicle (EV) market since launching its first car in 2008, other carmakers are quickly turning their fleets electric too.
General Motors has announced it will invest $35bn in electric and autonomous vehicle product development until 2025 and that it will phase out petrol and diesel cars by 2035. Volkswagen wants half of its vehicle sales to be electric by 2030 and nearly 100% electric sales by 2040. Audi will launch fully electric models only from 2026 and aims for all car sales to be electric by 2030.
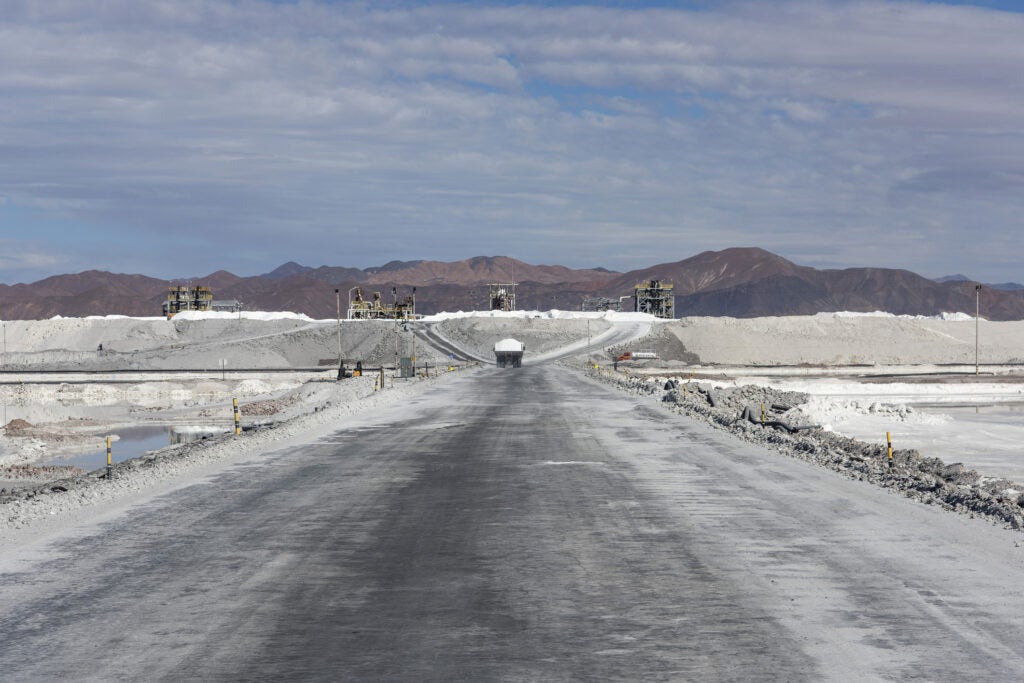
The transition to EVs is an important step in the move to a net-zero future. According to the IEA, more than 60% of passenger car sales must be EVs by 2030 for the world to be on track to net-zero greenhouse gas emissions by 2050. That is 18 times more EV sales than in 2020. By mid-century, all cars should be running on batteries or fuel cells.
Progress is under way. While total car sales dropped by 16% in 2020 due to the pandemic, the sales of battery electric and fuel cell vehicles increased by 29% compared with the year before. In 2021, sales of electric cars reached 6.6 million, more than double the sales from the year before.
Norway is ahead of other countries in the EV race. In 2021, 93% of new car registrations in the country were either all-electric battery vehicles or hybrids. Other markets have big ambitions. China wants 70% of passenger vehicles electrified by 2025 and 100% by 2035. The UK wants to phase out petrol and diesel vehicle sales by 2030, and all sales to be electric by 2035. Nine EU member states support the European Commission’s proposal to phase-out the sale of new petrol and diesel vehicles across the continent by 2035.
However, with the transition from fossil fuels to electricity comes challenges, especially in the EV supply chain. Several car manufacturers had to halt EV production in the last few months because of problems with the supply of microchips. In November 2021, Volkswagen halted production for a week at two German factories, and in February 2022, Ford suspended production at three assembly plants in the US and Mexico.
A new supply chain vulnerability index
A supply chain vulnerability assessment for battery EVs, using a methodology developed by Energy Monitor's parent company GlobalData, shows the countries with the biggest EV sales are also the countries with some of the biggest supply chain vulnerabilities, the exception being China. In the graphic below, the trade balance of the components and raw materials going into EV batteries has been indexed. The countries with the highest trade surplus have the highest scores, while the countries with the highest trade deficit get the lowest scores.
While Germany and the US have the second and third-largest EV sales, these countries also have some of the most vulnerable supply chains and are heavily reliant on imports in terms of EV batteries and raw materials, according to the GlobalData analysis. The other countries in the top ten of most registrations, including France and the UK, also score low on the vulnerability index.
The exception is China. The country had almost 1.2 million EV sales in 2020 and 3.4 million sales in 2021, while also dominating the market for EV batteries and materials. China has more than 70% of global EV battery production capacity and was responsible for $16.9bn in exports in 2020, according to GlobalData.
Lithium will grow the most
The EV industry’s rapid scale-up means demand for the commodities that go into batteries and vehicles is also expected to grow.
EVs can use different battery types. Most EV batteries are lithium-ion (Li-ion) batteries, however. The minerals needed for these can differ based on the chemistry of the cathodes, but lithium, cobalt, nickel, graphite and manganese are considered the key materials.
The challenge for the mineral sector lies in keeping up with this demand.
“Today, the data shows a looming mismatch between the world’s strengthened climate ambitions and the availability of critical minerals that are essential to realising those ambitions,” said Fatih Birol, executive director of the IEA in a special report on the role of critical minerals in clean energy transitions.
According to Birol, governments must act now to reduce the risks of price volatility and supply disruptions.
“Left unaddressed, these potential vulnerabilities could make global progress towards a clean energy future slower and more costly – and therefore hamper international efforts to tackle climate change,” he said.
Total critical mineral demand for EVs in 2020 was 0.4 million tonnes. Based on its Sustainable Development Scenario, the IEA predicts this demand to grow almost 30 times, to 11.8 million tonnes in 2050. Lithium is expected to see the biggest growth, followed by nickel and graphite.
The issue with meeting the demand does not lie in a shortage of reserves. According to the latest figures from the US Geological Survey, 89 million tonnes of lithium resources have been identified. On land alone, 25 million tonnes of cobalt resources and at least 300 million tonnes of nickel have been identified. Large reserves of resources of the two minerals have been found on the ocean floors as well.
Instead, the difficulty lies in creating new operational mines to produce useable minerals from those reserves. Moving a mining project from the discovery to the operational phase takes 16.5 years on average, according to the IEA. Growing environmental concerns and the lack of local support can delay or halt a project. In Portugal,(estimated to have Europe’s largest lithium reserves), locals are fighting new mining projects, leading to the shutdown of a lithium mining project in Montalegre.
The IEA's special report states it is unlikely the required mineral demand will be met based on today’s supply and investment plans. While some minerals are expected to have a surplus soon, the IEA predicts that in the mid to long term, demand will surpass expected supply from existing mining projects. Investments in new projects are needed to meet the growth in demand.
Reducing imports
Another challenge for the future supply chain is that many of the minerals essential for EVs are produced in only a handful of countries. More than half of the mineral supplies needed for EV batteries come from their top three producers.
In 2020, Australia was responsible for 48% of global lithium production. For graphite, China is the world’s main supplier, with nearly 79% of global production originating from the country. In 2020, the Democratic Republic of the Congo (DRC) supplied 69% of global cobalt.
The increasing demand for minerals has led to warnings about an increase in battery cost. The pack prices of Li-ion batteries hit an all-time low in 2021 of $132 per kilowatt-hour (kWh), due to better technology and economies of scale in production. A decade ago, the Li-ion pack prices were still more than $1,200/kWh. However, research company BloombergNEF’s annual battery price survey predicts costs could rise in 2022 due to rising commodity prices.
The IEA warns of the significant potential impact of raw material costs in the long term. “A doubling of lithium or nickel prices would induce a 6% increase in battery costs. If lithium and nickel prices were to double at the same time, this would offset all the anticipated unit cost reductions associated with a doubling of battery production capacity.”
Improving the security of supply of these minerals and reducing dependence on other countries is already a priority for many governments. In late 2020, the EU added lithium to its List of Critical Raw Materials, which contains a total of 30.
Maroš Šefčovič, a Commission vice-president, said at the time that Europe will need up to 18 times more lithium by 2030 and up to 60 times more by 2050 for EV batteries and energy storage. Currently, the EU supplies only 1% of its own demand for battery raw materials.
“We cannot allow to replace current reliance on fossil fuels with dependency on critical raw materials,” said Šefčovič in September 2020. “This has been magnified by the coronavirus disruptions in our strategic value chains. We will therefore build a strong alliance to collectively shift from high dependency to diversified, sustainable and socially responsible sourcing, circularity and innovation.”
[Keep up with Energy Monitor: Subscribe to our weekly newsletter]
Meanwhile, US President Joe Biden has rolled out an ambitious Build Back Better Act that includes the goal for half of new cars sold in the country in 2030 to be zero emissions. However, the same administration does not seem to be acting to secure a stable supply chain to achieve those goals.
Just last week, the government cancelled the leases of Twin Metals Minnesota to mine for cobalt, nickel and copper. Currently, there is only one operating mine in the US that produces nickel, and even though the country has large reserves of lithium, there is only one big operating lithium mining project, the Silver Peak Mine in Nevada.
Shortening supply chains
With the growing concerns about supply chains, carmakers themselves have started looking for solutions to secure EV production.
US manufacturer General Motors has developed a battery that needs 70% less cobalt. Other manufacturers are also exploring cobalt-light or free batteries, both due to the rising price of the mineral and humanitarian issues in the DRC. Human rights organisations, such as Amnesty International, have expressed their concerns about humanitarian issues in the DRC's cobalt mining industry, including weak regulation, human rights violations and pollution.
Tesla has shortened the supply chain by making deals with mining companies. The carmaker signed a deal with Talon Metals for nickel supplies in the US and with Australia-based Syrah Recourses for a supply of graphite. Other companies are initiating collaborations with battery-makers. Ford has announced plans to open battery factories in the US in collaboration with battery manufacturer SK Innovation. In Europe, Volvo and Northvolt have teamed up to build a joint battery manufacturing plant in Sweden.
“Our new battery plant will support our ambition to have a fully climate-neutral manufacturing network and secure a supply of high-quality batteries for years to come,” said Javier Varela, head of engineering and operations at Volvo, of the collaboration in a press statement.
“Through our partnership with Northvolt, we will also benefit greatly from an end-to-end battery value chain, from raw material to complete car, ensuring optimal integration in our cars.”