Not even Covid-19 could hinder the world’s roll-out of solar and wind power. Together, the two grew by 238GW in 2020, shows data from BP. This is more than the entire electricity capacity of Germany (224.6GW), and this growth is only set to accelerate.
From 2019 to 2030, generation from onshore wind will have to triple, solar quadruple and offshore wind increase six-fold for there to be a 50% chance of limiting global warming to 1.65°C, according to the International Energy Agency (IEA).
Discover B2B Marketing That Performs
Combine business intelligence and editorial excellence to reach engaged professionals across 36 leading media platforms.
But achieving net-zero emissions will take more than generating more power from renewables. Emissions produced during their development will also have to be neutralised, while end-of-life waste will have to be repurposed or recycled. This poses significant challenges.

“Although renewables are very low-carbon, the electricity they produce is not totally carbon neutral,” says Keith Whiriskey from the environmental NGO Bellona. “Reducing CO2 emissions in the manufacture of renewables, by using low-carbon steel, cement [and] plastics, will be necessary in a net-zero world.”
Embodied emissions mean the carbon impact of wind power is 10g of CO2 per kilowatt-hour (gCO2/kWh), while for solar it is 30gCO2/kWh, shows data from Bellona. For natural gas – which is the cleanest source of power from fossil fuels – the impact is 380gCO2/kWh.
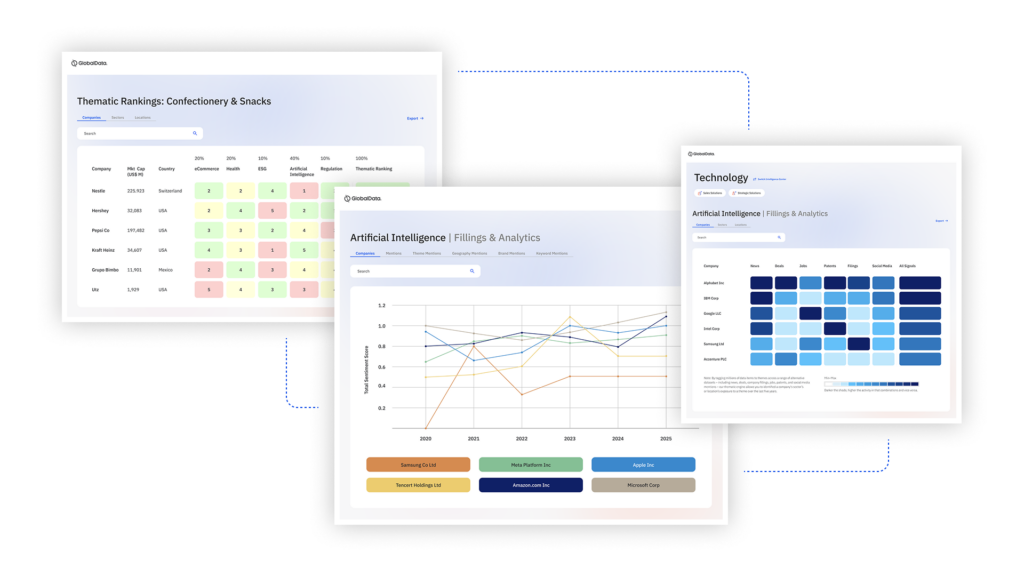
US Tariffs are shifting - will you react or anticipate?
Don’t let policy changes catch you off guard. Stay proactive with real-time data and expert analysis.
By GlobalDataPatrick Schroeder, a circular economy expert at UK think tank Chatham House, says the world’s rapid roll-out of renewables “has largely not considered end of life issues yet”.
“The low- carbon transition needs to be designed with a material focus, with everything designed with a closed loop mindset as it is installed,” he says. “Initially it was important simply to promote renewables over coal and other fossil fuels, but now that the transition is happening and is unavoidable, we need to think more about the circular economy.”
Sorting out solar
Solar PV panels are amongst the dirtiest renewable energies. This largely comes down to the high silicon content in the solar cells, says Meng Tao at Arizona State University, US, a sustainable solar expert.
Around 80% of the world’s silicon is created through an incredibly energy-intensive method called the Siemens process, which involves heating trichlorosilane gas to more than 1,10ºC. It was first carried out by its namesake company in the late 1950s. Since then, the energy required to produce 1Wp (‘watt-peak’ – a standard measure of solar power capacity) has fallen drastically, from 16kWh in the mid-1990s to 3kWh in 2020. However, this energy consumption remains significant, says Tao, particularly when the standard lifetime electricity output of 1Wp of solar capacity is just ten times that at 30kWh.
“People think that if you put solar panels on your roof you automatically have sustainable energy, but that is not true at the moment because the solar panels themselves are not sustainable," says Tao. "The silicon we use in solar cells is one of the most energy-intensive products we have.”
Tao adds that there are other methods, such as molten salt electrorefining, which can be used to purify silicon with much less energy. The level of purity needed for solar cells, however, as well as the comparative cost of other methods at scale, mean the Siemens Process remains preferable. Routes to lower-carbon PV power include improving the efficiency of the Siemens process and using thinner silicon wafers (research suggests their thickness could be reduced from the standard 180μm to 50–100μm). Raffaele Rossi from industry group SolarPower Europe maintains that technological improvements in the industry have been “rapid and continuous”.
"PV modules have a roughly 30-year lifespan", says Tao, after which they may no longer be economical. The industry is working to extend that lifespan. "It is not yet clear how long PV products could last", says Rossi, "given that wide-scale deployment of PV systems didn't begin until the early 2000s."
The currently expected lifespan and rapid roll-out of solar power mean it is likely a glut of panels will reach their end of life after 2030. It is hard to quantify this: in 2016, the IEA estimated that 78 million tonnes of solar panel waste would be created if 4,500GW were installed by 2050. By comparison, total e-waste from all sources amounted to 53.6 million tonnes in 2020, shows data from the Global E-Waste Monitor. The IEA forecasts that solar will actually grow to more than 20,000GW in its net-zero 2050 pathway.
Solar panels are difficult to recycle, due to the way minerals including lead, silver and silicon are combined to form the solar cell. Panels tend to get processed at traditional recycling plants where glass and metals like copper and aluminium can be extracted – but it is a “rudimentary process” that does not capture the elements of highest value, says Tao. If the solar cell then ends up in landfill, toxic materials such as lead leach out, creating environmental hazards.
There are a small number of dedicated solar cell recyclers who have developed methods of separating out the most valuable components. Waste company Veolia runs the world’s only commercial-scale silicon PV recycling plant in France, which grinds up panels and is able to recover low-purity silicon.
Tao himself owns a start-up, TG Companies LLC, which he says has a unique method of extracting “nearly 100%” of the high-quality lead, silicon, silver, tin and copper through a circular chemistry in order to cut down the chemical waste from recycling. However, it has been difficult to commercialise due to volatile mineral prices, making it hard to plan for any consistent financial return.
Working with wind
Wind power has among the lowest life cycle emissions of all renewable energies. This is the result of breakneck technological innovation that has seen turbines grow both significantly larger and more efficient. However, any emissions involved in manufacture, transport, construction and maintenance must nevertheless be neutralised if the world is to reach net zero.
Analysts at Bernstein Research have calculated that steel – at 62% – and aluminium – at 9% – account for most of offshore wind's emissions. Modelling by BloombergNEF has shown that building enough wind turbines to reach net zero by 2050 will involve 1.7 billion tonnes of steel, a figure just under the entire planet’s steel output (1.8 billion tonnes in 2020, according the World Steel Association).
The global steel industry produces around 7% of annual man-made emissions, says the World Resources Institute. Blast furnaces used to forge the metal require the combustion of coal to make ‘coke’, or purified carbon, but there are cleaner alternatives, such as using renewable ‘green’ hydrogen instead of coal, or recycling existing steel in an electric-arc furnace. Both these methods require considerable amounts of renewable electricity to be clean.
Swedish steelmaker SSAB AB is leading the way in the production of green steel, using hydrogen with the aim of commercially selling the world fossil-free steel by 2026. Growing confidence in emerging technologies can be seen in the number of steelmakers now committing to net zero, including giants like ArcelorMittal, Nippon Steel Corp, and China’s Baowu.
“As more companies and countries commit to net zero, they will begin to strategise [about] what they have to do in order to meet that target,” explains Feng Zhao from the Global Wind Energy Council (GWEC). “Momentum is building that will feed into the wind industry’s value chain.”
Wind turbines are typically installed with an expected lifetime of 20 years. In many countries, such as Germany, it is after this point that operators will lose state support, says Christoph Zipf from industry group WindEurope.
This does not necessarily mean those turbines will be taken offline: while 2021 has seen 4GW of wind capacity in Germany reach the end of its feed-in tariffs, the country has not witnessed significant decommissioning. According to Zipf, “a thorough service and maintenance regime” has prolonged the expected lives of many turbines. Moreover, “repowering” wind farms with new machines can “more than triple” their electricity output, providing a commercial incentive for many operators to prolong a plant’s life.
However, a time will come when all the world’s currently operating wind turbines are retired. The good news is that, according to WindEurope, 90% of the material mass of modern turbines already has established recycling streams, including steel, cement, copper wire and gearing. The challenge for the industry is recycling turbine blades, which are made from a composite material – usually reinforced carbon fibre or glass fibres – that allow them to be both light and extremely durable.
According to Zipf, the small volume of blade waste currently produced in Europe can be absorbed “by a single waste management company in Germany”, which grinds down the material and uses it as a substitute for sand in cement production. This processing can produce a “50% recycling yield”, say researchers from blade repurposing research specialists Re-Wind, with the rest ending up in landfill.
Re-Wind’s Emma Delaney has modelled how much material might be produced by all the blades currently operating worldwide. She assumes blades produce ten tonnes of waste per megawatt of capacity and have a 30-year lifespan. Her analysis suggests there will be more than six million tonnes of total blade material by 2050.
While such numbers are daunting, ongoing innovation means waste from blades will be less of a problem in the future.
“Circularity is central to the wind industry,” says John Wawer from leading turbine manufacturer Vestas. “It is important to not only be sustainable in the traditional way, by delivering clean energy, but also in a holistic way, thinking about the various aspects of our operations.”
The company currently plans to produce zero-waste turbines by 2040, an industry-leading ambition when it was announced in 2020. Vestas is working to increase the recyclability rate of hubs and blades from 44% today, to 50% by 2025 and 55% by 2030. In May 2021, the company unveiled a "game changer" blade material recycling technology it described as the “final step” towards fully recyclable wind turbines.
[Keep up with Energy Monitor: Subscribe to our weekly newsletter]
Meanwhile, Vestas competitor Siemens Gamesa unveiled a new recyclable blade earlier in September, in a move described by GWEC’s Zhao as “a milestone for the industry”.
These 81m blades are designed to allow recyclers to separate component materials more easily at end of life. At present, the increased price means it is a “feature product”, says the company’s Jonas Jensen, but this has not stopped three developers – France’s EDF, Germany’s RWE and the UK’s Western Power Distribution – from expressing interest.
For Jensen, championing the circular economy makes perfect sense. “The luxury of being a renewable energy company,” he says, “is that the innovative products and services you develop will end up being instrumental for decarbonising all kinds of sectors, from steel to transport, due to their ultimate reliance on renewable energy to produce electricity or hydrogen.”
Regulating for change
With innovation to reduce emissions and increase circularity, many in the industry are calling on policymakers to improve the business case for low-carbon products and recycling. “PV manufacturers should be given the right economic incentives to use renewable energy in their production process,” says SolarPower Europe’s Rossi.
The European Commission is currently preparing sustainable product policy measures under the Ecodesign Directive to motivate PV product producers to improve their carbon footprint, energy efficiency and circularity, addressing aspects such as recyclability and durability.
Under EU law, producers are already required to ensure all solar panels are recycled, with companies that put panels on the market also responsible for financing their end-of-life management. Although the EU does not require materials to be recovered with their original quality, it still compares very favourably with the US, where only 10% of panels are recycled.
“PV manufacturers should be given the right economic incentives to use renewable energy in their production process,” Raffaele Rossi, SolarPower Europe
In wind, Giles Dickson, CEO of WindEurope, has called on the Commission to introduce a Europe-wide ban on landfilling decommissioned wind turbine blades by 2025.
“Currently, only four European countries have such a ban in place: Germany, Austria, the Netherlands and Finland,” says WindEurope’s Zipf. “Wind turbine blades are non-toxic and landfill safe, but we want to lead on circularity and believe the blades contain valuable resources.”
Siemens Gamesa’s Jensen says that “regulation is a way to encourage companies to do the responsible thing”. His company is in contact with regulators to understand where the market is heading. “We see that as a society we are moving towards circularity, and so we also see that it makes good business sense to prepare for that now,” he says.