
With every year that passes, the hype around green hydrogen builds. Many analysts are now convinced that the gas is the missing link between renewable power sources like solar and wind, and hard-to-decarbonise sectors like heavy-duty transport and heavy industry.
The International Energy Agency (IEA) anticipates hydrogen demand will increase sixfold in a net zero by 2050 scenario, from 94 million tonnes (Mt) today to 530Mt. Already, major downstream technological progress is being made: fossil fuel-free green steel was produced using hydrogen for the first time in 2021, while 2022 saw the first fleet of hydrogen fuel cell trains start operating in Germany. There are now 100 pilot projects testing hydrogen for use in shipping, according to the latest hydrogen market report from the IEA.
However, the same report highlights how, for the time being, green hydrogen sourced from renewables remains very much a nascent industry: just 1Mt of low-emission hydrogen was produced in 2021, the vast majority using fossil fuels with carbon capture, utilisation and storage (CCUS).
A massive scale up in electrolysis capacity – to transform water into green hydrogen using renewable electricity – is required. This is in the works: S&P Global Commodity Insights currently projects electrolyser installations to grow by more than a factor of 2,000 from 0.5GW today to more than 1,000GW by 2050.
However, there remains uncertainty over what kind of electrolyser will ultimately be most widely used – as well as concerns over whether the Earth’s crust can provide sufficient minerals to scale up capacity.
Critical minerals concerns for green hydrogen
Many now think that proton exchange membrane (PEM) electrolysers are likely to become the dominant technology. These have the advantages of being smaller than alternative technologies, and also being able to work well with a flexible electricity supply – something that will be crucial if they are linked to variable renewable electricity supplies such as a solar or wind farm. The majority of green hydrogen demonstration projects outside of China use PEM electrolysers, according to the IEA.
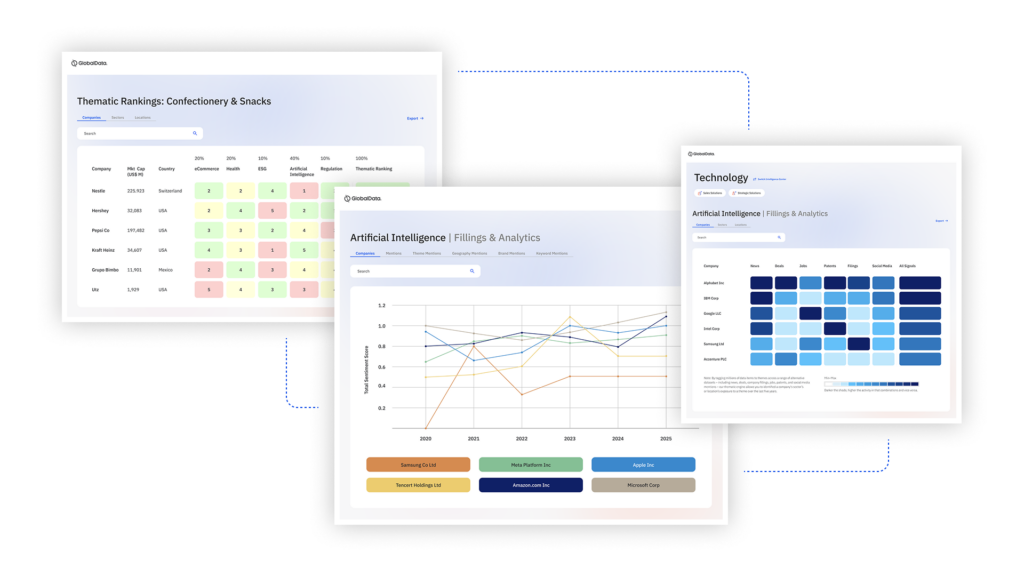
US Tariffs are shifting - will you react or anticipate?
Don’t let policy changes catch you off guard. Stay proactive with real-time data and expert analysis.
By GlobalDataHowever, as analysts have increasingly suggested that PEM will come to dominate the green hydrogen market, warnings have likewise increased that the world might not be able to meet the critical mineral requirements of the technology. This is because the anode in PEM electrolysers is made from an ultra-rare mineral called iridium, around which there are serious availability concerns.
Annual iridium production is only around 9 tonnes per year, according to S&P Global Commodity Insights. Production cannot easily be scaled up, not only because it is extremely rare (representing around 0.00000003% of the weight of the Earth’s crust) but also because there are no iridium-specific mines. Instead, the mineral is produced as a byproduct from mining platinum or palladium, minerals whose main use today is in catalytic converters in internal combustion engines (ICEs), and which therefore may see their demand fall in the coming years as ICEs are phased out.
“Meeting just the EU’s goals for green hydrogen production could by 2030 lead to demand for iridium for electrolysers that is several times current global supply,” wrote Ed Crooks, vice-chair of the Americas at the consultancy Wood Mackenzie, in a recent blog post. He added that such is the growing concern around supplies of platinum group metals – which include iridium – that the Biden administration has acknowledged it to be a “critical issue” in the development of a low-carbon hydrogen industry.
H2Pro: a new green hydrogen technology
One man who thinks he has found the solution to the iridium problem is Talmon Marco, an Israeli businessman and founder of the hydrogen start-up H2Pro.
H2Pro is developing a new hydrogen electrolysis method known as E-TAC (electrochemical, thermally activated chemical). Like PEM, E-TAC works well with a variable electricity supply, and can be produced in smaller, more mobile facilities. Unlike other hydrogen production methods, E-TAC’s electrolysis has two steps; the first electrochemical stage sees hydrogen released, but – unlike other methods – the hydroxide ions that are produced oxidise the anode, which is made of nickel, to create nickel oxyhydroxide. The second step sees the nickel oxyhydroxide anode react with water to spontaneously produce oxygen.

The two-step electrolysis does away with the need for a membrane, which is normally needed to separate the hydrogen and oxygen produced during the process. Eliminating the membrane should reduce the cost; Marco believes that his company will ultimately be able to produce green hydrogen for $1 per kilogram (kg).
“We were founded in 2019, and we are now in the process of commercialising our technology,” Marco told Energy Monitor. “We began with a beaker in a lab, but today we have a system producing 10kg per day, and by next year the figure will be 200kg.”
Other technological solutions
H2Pro’s biggest shareholder is Breakthrough Energy, the low-carbon innovation investment vehicle founded by Bill Gates, but even with this high-profile backing, there are doubts that E-TAC will be the panacea that H2Pro is promising.
There are two main issues: the first is that E-TAC may one day have its own critical mineral supply issues, given its use of the metal nickel. According to H2Pro analysis, producing five million tonnes of hydrogen per year (around 5.3% of current global demand, or 0.9% of net-zero demand) using E-TAC would require 75,000 tonnes of nickel. This compares to two tonnes of iridium, when using PEM.
Global nickel production in 2021 was 2.7Mt, according to the US Geological Survey, and known reserves stand at 95 million tonnes. If E-TAC was to scale up to provide all 530Mt of hydrogen required annually in a net-zero scenario, 8.3Mt of nickel would be needed each year, based on the figures provided by H2Pro – a situation that would evidently be unsustainable.
There is already concern that demand for nickel could outstrip supply, given the growing demand for nickel to produce the batteries that power electric vehicles, as well as the nickel used to create stainless steel.
The other problem with E-TAC is it remains an untested technology; the chemical reactions involved in the process are still being trialled, and gradually scaled up. “It is important to remember we are still in development,” notes Marco. “Only if it works – and we believe it will – will we have a cheaper and more efficient technology than the alternatives.”
Luckily, there are other green hydrogen technologies that could yet fill the gap if both PEM and E-TAC are found to be impractical.
Alkaline electrolysis is a more mature electrolysis technology that has been around since the 1920s. The technology has low capital costs, although current technology once again requires a large volume of nickel to work – around one tonne per megawatt (MW), says the IEA. Another drawback is that alkaline electrolysis requires a constant power source to work effectively, and requires a lot of space to produce hydrogen at capacity.
Solid oxide electrolysis cells (SOECs) are another method, and are currently being tested at a smaller scale. SOECs have high efficiency and low material costs (currently requiring 150–200kg of nickel per MW), although like alkaline electrolysis they require a constant power source, and like E-TAC the technology remains at an early stage of development.
With all these technologies, there is a strong likelihood that mineral requirements will decline as technology matures. Japanese conglomerate Toshiba, for example, recently announced it had developed a large-scale production technology for PEM electrolysis that could reduce the need for iridium by 90%.
Strength through diversity: critical minerals unlikely to hold up green hydrogen
What we have, then, is a burgeoning industry filled with different competing technologies and innovations. This diversity of solutions means that critical minerals are not likely to be the big issue some green hydrogen sceptics suggest they may be.
“All electrolyser technologies have strengths and weaknesses, meaning each technology can (over time) find the most appropriate applications,” an analyst from S&P Global Commodity Insights told Energy Monitor. “Companies must consider capital cost, durability, energy efficiency, heat input requirements, operating flexibility, system size, maintenance contracts. There will be many winners in this space.”
Peter Collins, from the lobby group Hydrogen Europe, agrees that “all technologies will be needed to accommodate for the variety of sectors and their specific needs and limitations.
“We welcome and encourage disruptive and promising concepts such as H2Pro – but it seems premature before claiming any particular technology will be the technology of the future.” He adds that “recycling of raw materials will be a significant aid in mitigating resource scarcity”, while other technologies like waste-to-hydrogen using thermal energy hold “huge potential”.
[Keep up with Energy Monitor: Subscribe to our weekly newsletter]
Ian Lange, from the Colorado School of Mines, says that technological developments have always run into bottlenecks resulting from mineral supplies, but there “has always been a substitute – and if not, new technologies will develop”. He adds, though, that there are other areas that should perhaps be more of a concern for the industry, such as competition from other technologies, or the difficulties developing reliable infrastructure that can transport the highly flammable, leaky and colourless gas.