Implementations of Carbon Capture Technology
Industry – from oil and gas companies to steelmakers and cement producers – is the world’s largest source of carbon emissions. According to the International Energy Agency (IEA), after allocating electricity and heat emissions to their final sectors, industry accounts for around 40% of global emissions. If the world is to have any chance of hitting net-zero emissions by 2050, the sector is going to have to find a way of capturing and locking away those emissions.
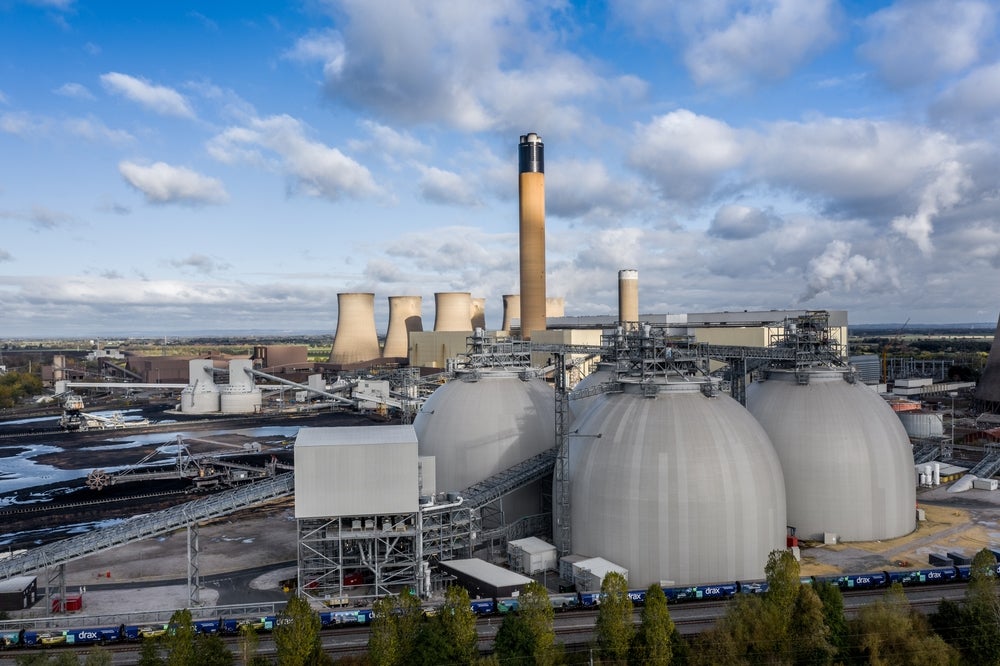
The race is on. On 19 April, oil and gas giant ExxonMobil estimated the market for capturing carbon and storing it underground will be worth $4trn by 2050. Exxon and other industry titans have been investing heavily in carbon capture, use and storage (CCUS) – with mixed results – since international bodies such as the Intergovernmental Panel on Climate Change (IPCC) identified the technology as key to mitigating the effects of global warming.
In its latest report earlier in April, the IPCC stressed that the only realistic scenarios for keeping within 1.5°C involve the full phase-out of coal and the use of technologies for CO2 removal.
CCUS: the key to net zero?
CCUS involves the capture of CO2 from fuel combustion or industrial processes, and its transport by ship or pipeline for underground storage in geological formations or for use as a resource to create products.
“This [CCUS] can be in industry – cement, steel, natural gas processing, hydrogen [production] etc – but also in power generation, such as coal and gas power plants,” explains David Lluis Madrid, a sustainable materials analyst at research company BloombergNEF (BNEF). “It doesn't necessarily have to be post-combustion,” he adds. "For example, in fertiliser production the carbon dioxide is released as a by-product.”
The CCUS project pipeline has been rapidly expanding. There are now 29 commercial and pilot projects in operation, 20 of which came online in the past two years, according to the Global CCS Institute, a Melbourne-based industry think tank. In just the first nine months of 2021, the global capacity of planned CCUS projects grew 50% to 111 million metric tonnes, which would triple the world’s current operating capacity.
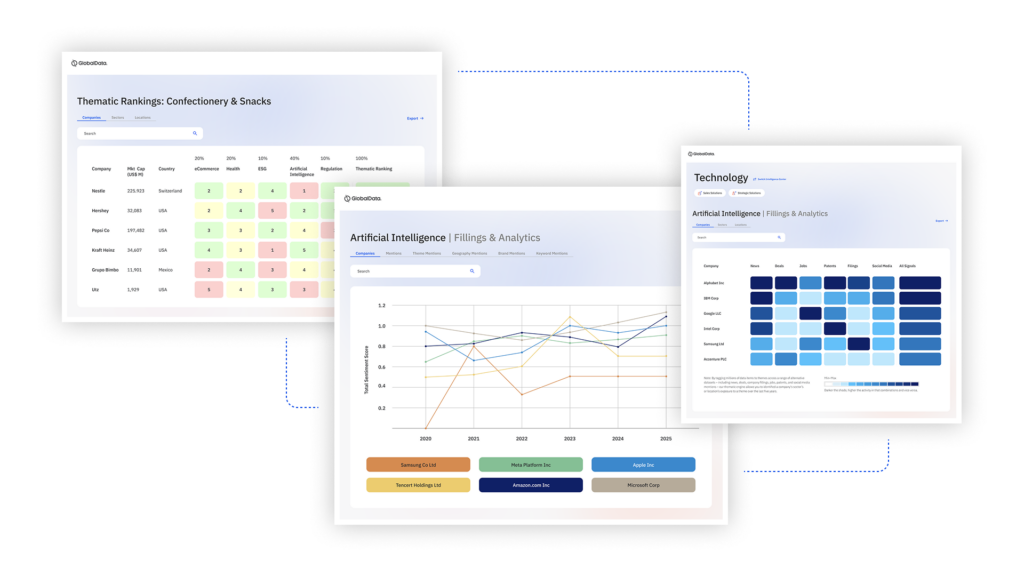
US Tariffs are shifting - will you react or anticipate?
Don’t let policy changes catch you off guard. Stay proactive with real-time data and expert analysis.
By GlobalDataOne of the key catalysts behind this growth was the publication of the IPCC’s landmark report in 2018, which highlighted the need to reach net-zero global greenhouse gas emissions by 2050 for a good chance of limiting global warming to 1.5°C. Three of the IPCC’s four pathways to net zero had CCUS at their heart.
CCUS will be crucial for sectors where emissions cannot be avoided completely, such as in heavy industry. The IEA estimates that to get to net zero, CCUS capacity will need to grow 40-fold by 2030, requiring a 50% capacity increase year-on-year.
That is a big ask. At present, captured carbon emissions amount to little more than 0.12% of energy-related CO2 emissions. Even though the technology has been around for decades, it has struggled to scale as capital costs have remained stubbornly high. Improving the economic and policy incentives, and building new revenues streams – such as finding new uses for the captured carbon or growing the carbon offsets market – will be essential for making CCUS affordable.
Capturing industrial emissions
CCUS technology has been around for years. In Europe, it was originally seen as a way for fossil fuel power generators to continue producing electricity using coal or gas, but the plummeting cost of renewable energy helped bring such projects to a halt. Europe's ambition to become the world's first climate-neutral continent has revived interest in the technology, but this time more in industry, rather than power generation.
In recent years, globally, CCUS has been applied most often in the gas processing, fertiliser and ethanol industries – despite the rate of carbon capture staying pretty consistent across all sectors at around 90–95%, according to BNEF’s Madrid. This is because those industries have the lowest cost of capture: they typically generate a pure CO2 stream that is stripped out as part of the production process. “For example, in gas processing, CO2 is stripped out to meet pipeline specifications,” says Guloren Turan, general manager for advocacy at the Global CCS Institute.
However, CCUS is starting to be applied to a wider range of industries where the capture cost may be higher – usually due to the lower concentration of CO2 in the flue gas – such as cement and steel production, as well as power generation. “Within power generation, natural gas plants are easier [to apply CCUS to] as the flue gas is cleaner than say for coal,” says Naoko Ellis, professor of chemical and biological engineering at the University of British Columbia in Canada. “Coal plants have a lot more impurities.”
HeidelbergCement is set to open the world’s first full-scale CCUS facility at a cement plant in Norway, and cement behemoth LafargeHolcim is working on CCUS with Schlumberger New Energy. In parallel, some of the world’s largest steelmakers, including ArcelorMittal, ThyssenKrupp, Nippon Steel and Posco, are turning to hydrogen and CCUS to realise their net-zero ambitions.
In fact, the clean hydrogen economy has become one of the main drivers of CCUS. Emissions-free hydrogen and its derivative fuels could be used to decarbonise hard-to-electrify transport such as ships and aircraft, heavy-emitting industries such as steel, aluminium and cement, and even home heating. The latter is hydrogen's most highly contested application.
Most hydrogen today is 'grey', meaning it is made from natural gas via a cheap but highly polluting process called steam methane reforming (SMR) – for every tonne of hydrogen produced, ten tonnes (t) of CO2 are released into the atmosphere.
However, the process can be decarbonised using CCUS to capture the resulting CO2, creating what is known as 'blue' hydrogen. In time, 'green' hydrogen, which uses renewable electricity to separate the gas from water, is expected to dominate; however, green hydrogen requires costly electrolysers to be built and consumes vast quantities of precious green power. Many have argued for a transition role for blue hydrogen, although soaring gas prices compounded by the Ukraine war suddenly make that a less attractive proposition.
At the moment, the biggest players in the CCUS space are the oil and gas majors and LNG exporters. Much promise has been placed on the shoulders of carbon-neutral LNG, although its green credentials remain a topic of heated debate.
The world’s existing CCUS capacity is highly concentrated in natural gas processing plants. In most cases, the captured CO2 is used for enhanced oil recovery (EOR), the practice of forcing more oil from a well that has already yielded its low-hanging fruit. According to Energy Monitor's parent company, GlobalData, 74% of operational CCUS facilities are still incentivised by the additional economic value generated from EOR – a practice whose environmental sustainability has been called into question.
US dominance and EOR
Regionally, the US dominates the CCUS landscape. North America accounts for approximately 50% of active CCUS projects, most of which are in the US. This is partly down to the size of its natural gas market, which allows for large-scale processing that makes CO2 separation economical, and partly because the country has had the most supportive policies for CCUS deployment, including the 45Q tax credit that allocates $50 per tonne for every tonne of CO2 that is stored underground.
There is growing interest in other parts of the world, however, particularly in continental Europe, the UK and Japan. Gas exporters in the Middle East are also eyeing the blue hydrogen market, and the big coal-fired power generators, notably India and China, are starting to invest in CCUS infrastructure.
The North Sea has become a focal point for blue hydrogen, led by the UK and Norway. The UK wants to become a world leader in CCUS, removing ten million tonnes of CO2 by 2030, and aims to produce 5GW of blue and green hydrogen in the same time frame. The country’s £1bn ($1.26bn) CCUS infrastructure fund is looking to develop two “hub and clusters” by 2025 and another two by 2030, which will link a number of emitters to a shared pipeline and storage site to build economies of scale.
Concretely, H2H Saltend at Humberside on the north-east coast – for easy access to large storage sites under the North Sea – will produce blue hydrogen, and Net Zero Teesside will be a integrated gas-fired power plant and carbon capture project. HyNet is developing a similar project in the north-west.
Norway’s Longship carbon capture project and Northern Lights transport and storage scheme will initially capture 400,000t of carbon before ramping up to 1.5 million tonnes a year by 2024. It eventually aims to expand capacity to five million tonnes a year and to sequester carbon from customers all over Europe.
Evolving technology
So far, the technology that has been most deployed to capture carbon is liquid absorption with amine-based solvents, but novel technologies are testing new solvents, or other types of capture such as solid adsorbents or membranes. “At the moment, there isn’t a clear winner,” says BNEF’s Madrid. “Novel solutions still need to be deployed at scale and each have pros and cons: some require less energy, others less sorbent amounts – and consequently smaller facilities – as the same amount of sorbent will be able to capture more CO2.”
There is some low-hanging fruit, however. When CCUS is applied to grey hydrogen production through SMR, it can capture 85–90% of emissions, but an alternative production technology, autothermal reforming, allows for 96–97% capture and will likely be used in new plants, says Ellis at the University of British Columbia.
CCUS technology company Svante is also developing a carbon capture technology using a structured solid sorbent to bind the CO2. The solid sorbent is placed in a rotating column that captures diluted CO2 from flue gas and releases concentrated CO2 when it is exposed to steam. The Canadian company is currently scaling up its operations and working with hard-to-abate industrial emissions, such as in the cement and steel industries.
Italy’s Saipem, on the other hand, is developing carbon capture technology it calls an “industrial lung”, which uses a naturally occurring enzyme to capture CO2 from flue gases and turn it into pure CO2 for use as a chemical feedstock for building material and fuels. Note that although carbon capture and use can reduce, recycle or even remove emissions from the atmosphere, its role in climate action depends on the carbon’s origin and destination.
High cost barriers
Beyond debate over its net impact on climate change, the CCUS industry faces other challenges. Retrofitting operational facilities with CO2 capture technologies can be a complex, expensive and often energy-intensive endeavour, according to John Kent, chief energy transition officer of Kent, a Dubai-based engineering company specialising in CCUS.
Each project is unique in its design and size and has different installed equipment types that may or may not support emissions monitoring. This can complicate the installation or modification of capturing technologies, thereby leading to cost escalations. Besides, these facilities need to be supplied with additional power to operate the CO2 capture units, which may create additional challenges along the value chain.
[Keep up with Energy Monitor: Subscribe to our weekly newsletter]
On top of that, the prevailing low penetration of CCUS technologies worldwide inhibits the project economics, making retrofitting “less viable for now”, says Kent. Despite these challenges, a number of coal-fired power plants have been retrofitted in the last ten years to enable large-scale CO2 capture using amine-based solvents. However, these technologies have proved to be extremely energy intensive. As a result, there is a high-cost barrier in using them to cut coal-fired power plant emissions. CCUS deployments at gas-fired power plants have experienced similar cost issues, even though the technology is commercially proven and new amine formulations are being developed.
“The application of carbon capture to gas streams with dilute CO2 concentrations, such as from power generation, is more costly due to the laws of thermodynamics,” explains Kent.
In 2020, the world’s largest CCUS plant, the Petra Nova facility in Texas, shut down after becoming commercially unviable. Although the plant’s technology performed relatively well, the EOR, for which Petra Nova’s captured carbon was used, fell victim to a sharp decline in oil prices caused by Covid-19. Because EOR is more energy-intensive than conventional oil extraction, it needs high oil prices to remain commercially viable.
Similarly, Chevron has had a troubled start with its flagship Gorgon CCUS project in Australia. Under the terms of the project’s approval, the oil and gas major is required to sequester at least 80% of the CO2 emissions released from the reservoirs that feed the Gorgon LNG plant over a five-year period. While the project has been designed with a four million tonnes per annum injection capacity, Chevron admitted in July 2021 that the project had only injected five million tonnes of CO2 since its long overdue start in August 2019.
An urgent need to scale
Looking ahead, additional policy and economic incentives will be needed to develop CCUS to a scale where it contributes to the world’s net-zero ambitions. As well as investing in capture technologies, additional investment is needed to develop transportation and storage-related infrastructure. The recent amendment of the EU’s Trans-European Networks for Energy Regulation to include CO2 storage as well as CO2 transport modalities other than pipelines – such as shipping, rail or truck transport – should help with that. Industries need frameworks that align economic incentives with climate goals and regulations.
“CCUS technology is proven and established. The real challenge is economic,” says Kent. “Carbon capture is generally a pure cost for industrial operators, and in the absence of a robust, long-term carbon price, that cost is prohibitive.” For Kent, the single largest factor that could ignite broad carbon capture adoption is a global carbon tax. “That would provide the investment certainty required for this proven technology to have the needed critical impact.” In early 2022, carbon prices in the EU have hovered around the $100/t mark that modelling from the likes of consultancy Wood Mackenzie suggests CCS projects in the power sector require.
The 29 commercial CCUS facilities currently in operation have a total capacity to capture and inject 40 million tonnes per year – roughly equivalent to taking eight million cars off the road. There are an additional 141 CCUS projects currently under development, but to get to net zero by 2050, the IEA forecasts current capacity will need to be scaled up by at least 100 times over the next 30 years. “We need CCUS as one of the main tools for emissions reductions,” concludes Ellis. “With the carbon tax or other policy instruments coming in, the growth of CCUS is predicted to be high. However, we do need to make decisions with the necessary urgency and time frame in mind.”