Decarbonising Steel: The Four-Horse Race
The steel industry accounts for roughly 8% of global CO2 emissions. The sector is considered critical to the world’s net-zero transition, given the material is essential to many clean technologies, from wind turbines to electric vehicles. The problem is, steel is also considered a ‘hard-to-abate’ industry due to the challenge of electrifying production and the costs of the transition. Decarbonising steel in line with the Paris Agreement means the industry must cut emissions by 93% by 2050.
“The need to decarbonise the steel sector emerges from the demand and supply side push,” says Malan Wu, head of steel and raw material markets at consultancy Wood Mackenzie. “The end users are planning to gradually abandon the consumption of conventional, emissions-intensive steel products and switch to greener alternatives. On the supply side, steelmakers are gearing up to cater to emerging green steel demand and improve their ESG credentials by proactively decarbonising the steelmaking process.”
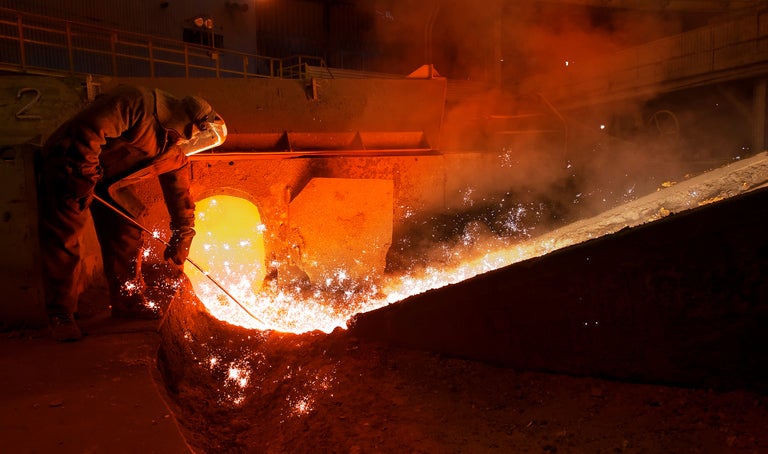
An understandable ripple of excitement reverberated through the industry when it emerged in October 2022 that US green steelmaker Electra had scooped $85m in backing from an array of high-profile investors, including the likes of Amazon and Bill Gates’ Breakthrough Energy Ventures, to scale its zero-emissions technology. Electra claims its pioneering iron ore and steelmaking process emits zero CO2 emissions while also holding the potential to become cheaper than existing fossil-powered methods.
Electra has developed an electrochemical process to refine iron ore to high-purity iron that lowers the process temperature from 2,912°F (1,600°C) to 140°F (60°C), replaces burned coal with variable renewable electricity and displaces commercial ores with lower-grade ones that are not being used today or are treated as waste. The company plans to complete construction of its first iron ore refining pilot plant in Colorado, US, in 2023. Its broader aim is to have a commercial-scale plant up and running before the end of the decade.
However, Electra’s breakthrough technology is just one of four that are competing for the green steel crown. Which will prevail in the decarbonising steel race depends on who you ask and when you ask them. The frontrunner is changing by the year, but one thing is certain: the race still has a few twists left.
Decarbonising steel
Steelmaking today is split into primary and secondary streams. The secondary stream refers to recycling steel from scrap metal. Around 70% of steel comes from primary production. The dominant technology today involves producers using coking furnaces to heat coal to make coke, which is then put into a blast furnace with iron ore. The coke is converted into carbon monoxide, which extracts the oxygen from the iron ore, leaving elemental iron, which melts to the bottom of the furnace. That liquid iron is then sent on to the basic oxygen furnace to have its carbon level set, which makes it steel. Next, it is sent to a ladle furnace – or ‘refining stand’ – to be mixed with nickel, magnesium, chrome and other elements to make it stainless steel.

“Most of the emissions come from that first step: getting the oxygen off the iron ore,” says Chris Bataille, adjunct research fellow at the Columbia University Center on Global Energy Policy. That is where the clean alternatives come in. Instead of blast furnaces, a technology was developed in the 1970s called Direct Reduction of Iron (DRI), where producers pelletised the iron ore before running synthetic gas (hydrogen and carbon monoxide) through it. The synthetic gas takes away the oxygen as steam, leaving solid elemental iron, which a producer can then sell or melt in an electric arc furnace.
To decarbonise DRI, producers can add carbon capture and storage (CCS) technology to catch the emitted CO2. Or, if they have an external heating source, they can use pure hydrogen instead of coal, a process called HDRI – this is the decarbonising steel technology that has probably received the most investment up to now.
Alternatively, there are two types of electrolysis technologies. In aqueous electrolysis (AE), as used by Electra, iron ore is submerged in acid and zapped with electricity, making the oxygen bubble off. In molten oxide electrolysis (MOE), electrodes are placed in powdered iron ore and a high current is run through it until it melts, and the oxygen comes off.
“We just need one of these technologies to work – and at a reasonable rate,” says Bataille, who was one of the lead authors of the industry chapter in the latest report from the Intergovernmental Panel on Climate Change.
Electra has a proof of concept but has yet to reach full commercial scale. The primary proponent of MOE is Boston Metal in the US. “A couple of years ago, they developed a proof of concept, but nobody’s heard anything from them since,” says Bataille. “The hope is they are close to hitting commercial scale.”
“Hard to pick”
Of the four competing technologies to decarbonise steel, DRI with CCS and HDRI are closer to commercial scale than the electrolysis technologies. “The hope for 30 years was that CCS could simply be attached to blast furnaces, but that is just not panning out,” says Bataille. Instead, there are versions of HDRI at the finance and planning stage across Europe, for operation somewhere between 2024 and 2030.
For example, H2 Green Steel and EIT InnoEnergy are developing a “giga-scale” green hydrogen-fuelled steel production facility in northern Sweden. Production will begin in 2024 and, by 2030, the companies forecast annual production capacity of five million metric tonnes of CO2-free steel. “When it comes to green steel, the Swedes are the leaders in the space, followed by the Germans and Austrians,” says Bataille.
On the other hand, the electrolysis technologies are more modular than their competitors. “That is a big advantage: you don’t have to have these big megatonne-level facilities as you do for HDRI or blast furnaces,” says Bataille. They also require less energy to drive the process; they are about 30–40% more efficient than HDRI.
The problem is that the electrolysis technologies require much more so-called “must-run” electricity for a tonne of steel, particularly MOE, so they are exposed to fluctuating power prices. This is where HDRI has the advantage. Sweden’s SSAB, for example, is building an underground cavern, where it will store hydrogen it has created using off-peak North Sea offshore wind, to be used by SSAB’s steel plant as and when needed.
This “fascinating world” is ever changing, admits Bataille. In 2016, the green-steel frontrunner was an advanced CCS technology called HIsarna, which collapsed the blast furnace into a basic oxygen furnace; you did not require coke anymore, just coal and oxygen and CCS. “Very rapidly, that technology went into the doldrums, and we never heard anything from it [again],” recalls Bataille. Then in 2018, HDRI came to the fore. Soon after, Boston Metal introduced MOE with much fanfare – but then went quiet. Now there is Electra with AE. “For the electrolysis approaches, it looks like Electra's AE technology is more advanced, but two years ago that would have been Boston Metal’s,” says Bataille. “It is very hard to pick, to be honest; green steel is a very secretive world.”
However, the fat lady, as they say, is yet to sing. “[AE] works for [decarbonising] niche metals like zinc, but decarbonising steel will involve producing hundreds of millions of tonnes a year; that is a heck of a lot of water and acid,” says Adam Rauwerdink, Boston Metal's senior vice-president of business development. “Some of the technologies are using membranes similar to those in a flow battery – there is a lot of complexity there that we just don't think can be done at the scale needed to move the needle for steel – and, as with HDRI, there is also potentially restrictions on the grades of iron ore that can be used.”
[Keep up with Energy Monitor: Subscribe to our weekly newsletter]
Each approach has its challenges to overcome. For HDRI and the electrolysis technologies, there is the simple matter of finding enough clean electricity to power the processes. At present, every industry is trying to decarbonise as quickly as possible, so the demand for clean electricity is sky-high and rising, but building new wind farms and solar plants takes time.
“Today, around one-sixth of global coal goes into steel production,” says Rauwerdink. “No matter how efficient you are per tonne, if you are going to replace that entire market and electrify it, you will need a tremendous amount of electricity.”
That is most problematic for HDRI, because when you convert electricity into hydrogen, you lose around 30% of it. “Globally, there will be a limit on clean electricity and hydrogen for at least a couple of decades,” says Bataille. “It will be expensive to get hold of, so anything you can do to reduce your power costs is going to have a big impact on your product price.” That is where SSAB’s North Sea bunker may pay dividends. However, for a country like Germany, with a much larger power demand than Sweden’s, and without the hydropower dams to fall back on, there is “a real question mark over where they are going to get all the hydrogen for their HDRI”, says Bataille.
Scaling up
Time is of the essence. For the steel industry to reach net-zero emissions by 2050, at least one of these green steel technologies will have to scale at an unprecedented rate. When it comes to the electrolysis techniques, Bataille believes AE will start to hit the commercial market, replacing existing blast furnaces, in the late-2020s and MOE in the early-2030s, but “HDRI has at least a ten-year lead on the electrolysis technologies, if not 15 to 20,” he says.
Rauwerdink, as one might expect, is more bullish about MOE’s prospects. Boston Metal plans to have a demonstration plant up and running in 2025–26. “If that is successful, we think it is about a three-year cycle to build plants, so by the end of this decade, you could have the first large-scale, gigatonne-scale plants coming online.”
All this will require vast levels of public and private investment. A recent report from Wood Mackenzie found that decarbonising the steel and iron ore industry by 2050, in line with the Paris Agreement, will require $1.4trn of funding and revolution across every stage of the value chain.
One of the largest recent investments in green steel technology came from Germany’s Thyssenkrupp, one of the world’s oldest steelmakers. In September 2022, the company announced it will spend €2bn to replace blast furnaces in its Duisburg plant with HDRI shafts. The plant, with a capacity of 2.5 million metric tonnes, will thus avoid the emission of 3.5 million metric tonnes of CO2 per year. “It is the largest [green] steel project globally – it is really big,” says Bataille.
Despite the daunting uphill challenge facing the industry, it is hoped that the recycling of scrap metal may eventually be scaled up sufficiently to take some of the pressure off these primary production technologies.
“In the long run, the hope is once we have lots of recycled scrap and only need a little bit extra primary iron, we can just make that with the two electrolysis routes when needed,” says Bataille. When that will come to pass, however, is anyone’s guess.