The European Commission estimates that demand for electricity will more than double by 2050 and half of that will come from wind. Companies like RWE and Ørsted want to triple and quadruple, respectively, their offshore wind capacities over the next decade. Yet the sheer amount of renewable energies needed to get on track to 1.5°C remains mind-boggling. At COP26 in Glasgow this month, a Global Renewable Energy Alliance was born to tackle an estimated 29% shortfall in the deployment of these technologies by 2030.
It is not just hard-to-decarbonise industries like steel, glass, paper and cement that intend to innovate their way out of the climate crisis. The wind industry is coming up with its own breakthrough technologies.
“What made us successful in the past won’t in the future,” said Anne Vedel, senior vice-president for product solutions and integration at Vestas, the Danish seller, installer and servicer of wind turbines, in Copenhagen on 22 November. She was addressing a group of journalists on a tour of the city’s wind energy highlights on the margins of industry association WindEurope’s annual conference, Electric City 2021, in the Danish capital.

There are three challenges facing the wind industry, Vedel said. One, scaling up annual installed capacity: this needs to catapult from 93GW in 2020 to 390GW by 2030, according to the International Energy Agency’s net zero 2050 road map. Two, larger turbines: the industry is getting to the limits of being able to efficiently install and run a turbine without “rethinking turbine architecture”, Vedel said. Finally, the best installation sites are taken. In product terms, this last point creates a need for “more differentiated offerings” that take into account local climatic conditions and grid connection possibilities.
Vestas’s answer to all three challenges is modularisation. Being in Copenhagen this invites an immediate comparison with Lego, but others in the wind sector evoke the car industry. The point is to be able to come up with a wide variety of product configurations with fewer unique components per variant, Vedel explained. It boils down to creating economies of scale while enhancing customisation, to bring down prices while enabling a faster, wider roll-out.
The idea has taken a number of years to come to fruition. The company started isolating components nearly ten years ago, back in 2012. It also started thinking about how to standardise the interfaces between them. The first modular onshore turbines created via the EnVentus platform were introduced in 2019. The first modular offshore turbine – the V236-15.0MW – followed earlier this year. It is the world’s largest wind turbine to date, but Vestas was not done innovating just yet. In mid-November 2021, the company announced another milestone: a modular nacelle.
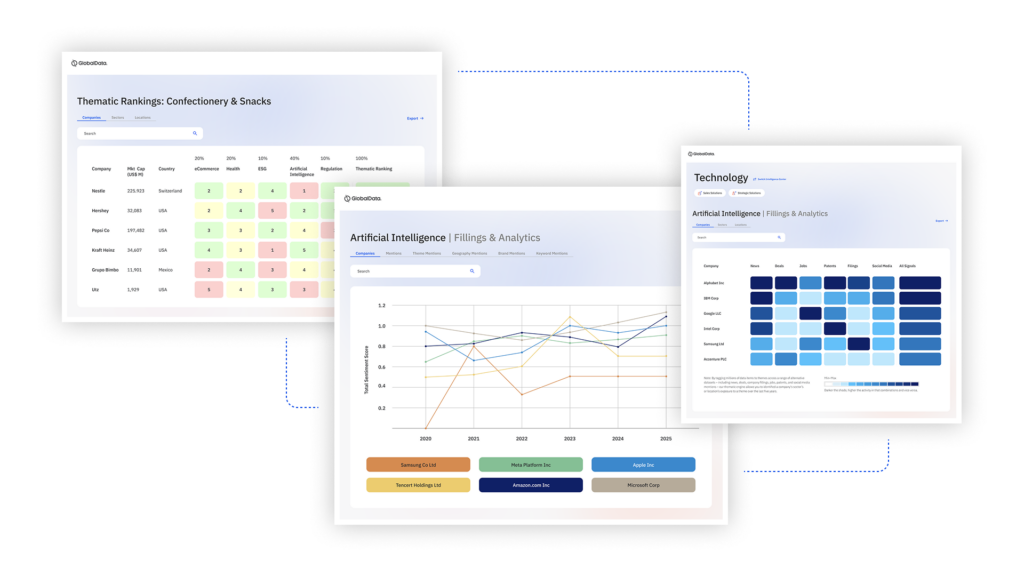
US Tariffs are shifting - will you react or anticipate?
Don’t let policy changes catch you off guard. Stay proactive with real-time data and expert analysis.
By GlobalDataA wind turbine’s nacelle is the horizontal, rectangular box at the top of the tower to which the rotor with blades is attached. It is a box that houses the ‘engine’ of the turbine, including the generator, gearbox, drive train, brake and control electronics. What Vestas has done, Vedel explained, is take the EnVentus components and rearrange them into a main unit and ‘click-on’ side compartments.
“As turbine components become larger and more efficient, they can also create logistical challenges to the expansion of wind power to all parts of the world,” explains Vestas’s chief technology officer Anders Nielsen. To make turbines more transportable, the modularised nacelle units are designed to meet general logistics industry standards. That is, they can be transported in regular containers by road, rail and sea, and do not require special handling.
The idea is also to enable more functionalities by adding or removing side compartments as needed. Using a simple click-on system, “the modular concept facilitates smart servicing solutions and opens up upgrade and innovation possibilities over the lifetime of the operating asset”, says Nielsen. A side compartment could contain a service crane, for example, that would alleviate the need to haul in an enormous outside structure to do a repair. In future, energy storage in the form of a hydrogen-producing electrolyser could be added to a wind turbine via a side compartment.

“The idea is that incremental changes to [modular] components enable us to scale without installing a new turbine every time,” summed up Vedel. “Compartmentalisation lets us address the infrastructure challenge and introduce new functionalities.”
The modular nacelle units are intended for use across onshore and offshore turbines. The innovation is already built into the V236-15.0MW offshore turbine unveiled earlier this year and it is part of the V162-6.8MW onshore turbine announced on 23 November. The plan is to extend the modularised design to the entire turbine, as well as offerings at the level of the wind park, including power plant controls and adjacent technologies like storage and power-to-x.
Greater standardisation will enable the wind industry to contemplate the kind of scale-up expected of it. Sheri Hickok, CEO of onshore wind international at GE Renewable Energy, told the Electric City conference that blade manufacture today is still “craft labour”. Getting Europe to the 1,000GW of onshore wind it needs for climate neutrality in 2050 means making 36 blades every day for the next 28 years, she said. That demands commodification, as well as automation and digitalisation. More common components means more validation time, which means more reliability, Hickok added.
Modular, standardised components of the kind Vestas is introducing should result in economic but also environmental savings. For example, they minimise the need for specialised transport, heavy equipment like cranes, specialised moulds for particular parts and the need to replace entire nacelles. This fits with an emerging quest for zero-impact renewable power.
"LCOE is done."
Competition on cost will remain important, but, just as has been suggested for batteries, some believe Europe could differentiate its wind products going forward with a 'green' edge.
Companies like Vestas are investing heavily in full value chain sustainability. The Danish turbine-maker has pledged to be carbon neutral by 2030 – without offsets. By the same year, supply chain (scope 3) emissions should be down by 45% per megawatt-hour. Scope 1 and 2 emissions hotspots include 4,000 service vans – by 2025, all new service vans should be electric vehicles or run on renewable fuels – and vessels, for which Vestas is also exploring alternative fuels. The latter are important with the offshore business being brought back in-house. The company aims to develop a fully recyclable blade by 2030 and zero-waste turbines by 2040. Its suppliers are due to set green goals for 2030 by end of the year and their suppliers should do the same by the end of 2022.
“We should expand the narrative beyond LCOE [levelised cost of electricity],” said Javier Rodriguez Diez, executive vice-president and chief sustainability officer at Vestas at the Electric City conference.
Some policymakers believe competitive auctions for public support should evaluate projects on more than just cost. Tinne Van der Straeten, Belgium’s energy minister, elaborated: “There is competition. I have other objectives when I do an auction. I want the project to be realised.” She – and others – argue that more citizen engagement is crucial to the further roll-out of renewables. Belgium will launch a market consultation on its auction mechanism in early 2022. Van der Straeten explained: “I am confident on the price issue. LCOE is done. I will be developing a national conversation on how we can make sure citizens participate [in renewables projects] and sustainability.”
Not everyone believes cost needs balancing out with other concerns in auctions. Andreas Feicht, secretary of state at the German Ministry for Economic Affairs and Energy, said: “We lost the solar PV industry [to China] because we didn’t put too much pressure on prices. Competition – this is true in the car industry too – is high. As long as something plays into cost efficiency, it should play into the auction mechanism.” If the pressure is taken off cost, “we have to accept higher prices and people do not want this”, he added.
Vestas is innovating to tick all the boxes, and therefore taking a shot at a faster, bigger roll-out of wind power that is also greener.