As the world scrambles to add enough renewably generated energy to the grid to meet ambitious net-zero targets, the wind sector is continuing to grow.
Fixed offshore wind farms are already harnessing energy from the coast’s high wind speeds. However, further away from shore lie two valuable resources: windier conditions and vast swathes of space.
The answer appears to lie in the floating offshore wind sector, but innovating in the ocean presents a host of challenges. An estimated 80% of wind resources are in locations where the sea is over 50m in depth. Deep water makes fixed wind structures unrealistic, but turbulent and changeable conditions complicate plans for floating wind.
While the floating offshore wind sector is in its infancy, innovation is pushing at the doors of opportunity. The Global Wind Energy Council (GWEC) reported in August 2023 that the global floating offshore wind pipeline had doubled since August 2022, reaching 240GW, although it caveated the progress by predicting that commercialisation was unlikely before 2030.
Mooring and hydrodynamics: planning for the water
Fixed offshore wind turbines are usually installed in water depths of up to 60m, but floating offshore wind turbines can be located much further out to sea. At Hywind Tampen floating wind farm – the deepest of the four existing ones in Europe – the turbines are located approximately 140km offshore in water as deep as 300m.
Mooring lines are responsible for securing floating wind turbine structures to anchors on the ocean seabed. Lines are usually made with a combination of chains (on the upper and lower sections), and synthetic rope (for the middle section), and they are connected to anchors that sit either on or below the seabed.
Speaking to Energy Monitor earlier this year, Dr Zaibin Lin, lecturer at the University of Aberdeen, said of the complex considerations inherent to mooring plans: “We have to restrain the motion of floating structure. These structures need to be moored – restrained – using a mooring line to limit motion. The line itself contains the tension force, which we call a mooring force.”
He explained that when engineering floating wind, the mooring force is predicted along with the six degrees of freedom – surge (forward/backward), sway(left/right), heave (up/down), roll, pitch and yaw. Designing a mooring system that can withstand the harshest elements at sea then requires the consideration and modelling of all of the potential forces which wind and water might exert on a structure.
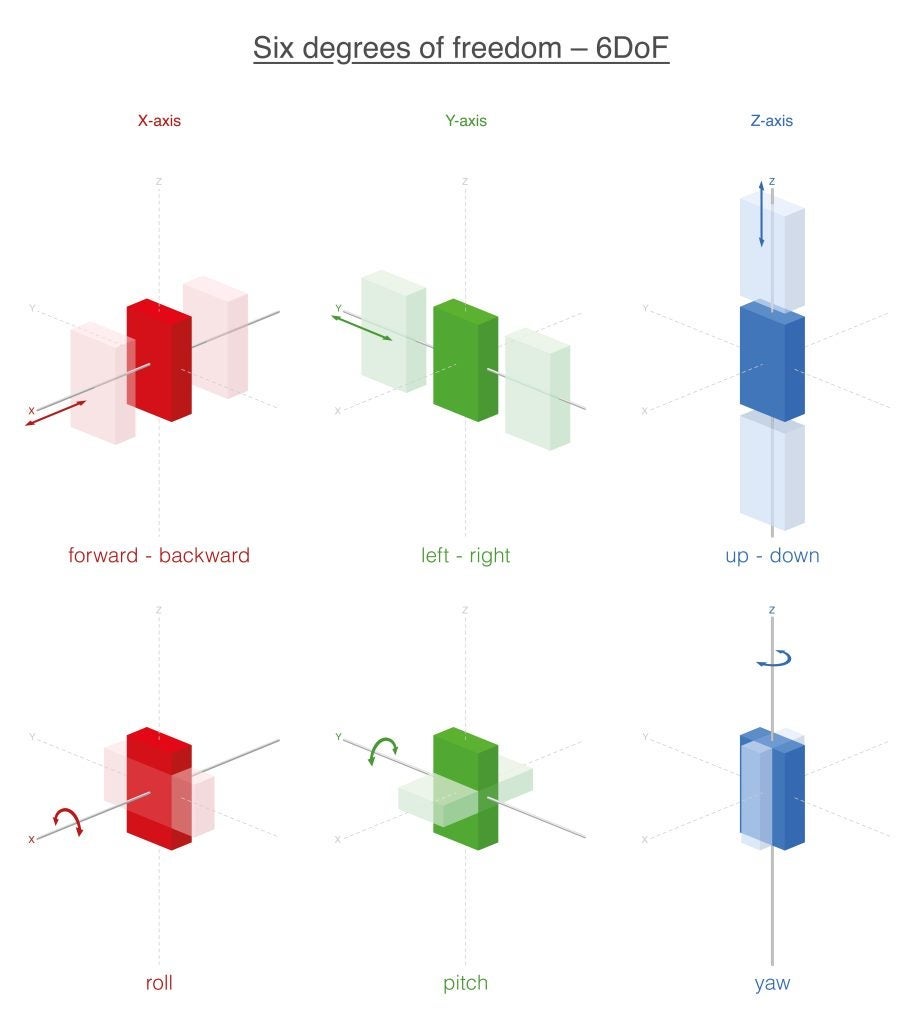
Anchoring: the options
To secure floating wind turbines, there are four primary types of anchors: drag embedment anchors, suction pile anchors, driven pile anchors and gravity anchors.
Made of concrete and shackle, gravity anchors tend to be unpopular due to their massive weight, which is usually between 600 and 1,000 tonnes. Drag embedment anchors are made of welded steel plates, and represent the cheapest solution, although they are only suited to areas with a sediment-type seabed. The anchors are launched from an anchor-handling vessel (AHV) using winches and a stern roller and are usually around 6m³ in size, weighing between 30 and 40 tonnes.
Suction pile anchors are suited to harder ground and are embedded using a combination of the anchor’s own weight and a remotely operated vehicle (ROV), which pumps water out of the pile to create a suction-effect. Usually around 35m in height, suction pule anchors weigh between 60 and 100 tonnes, and are installed using cranes that place them on the seabed.
Cranes are also used to deploy driven pile anchors, which are then embedded using an impact or vibro-hammer. Driven pile anchors are usually between 40 and 100 tonnes weight and around 40m in height. They are best suited to the hardest, rockiest ground.
Case study: X1 Wind's PivotBuoy
Securing the floating wind turbines is the first challenge, but it is accompanied by a second: efficiency. Fixed structures usually include an anemometer to asses the direction of the wind, and the nacelle and blades will move (yaw) to face the wind and maximise energy generation.
On the ocean, floating structures must contend with rougher seas and more extreme weather patterns, including major storms. This creates a dichotomous dilemma: how to secure a turbine against the elements but enable it to move with the wind.
X1 Wind recently won a Delta Gold award for the best industrial design in the ‘Outdoor Equipment’ category with its PivotBuoy technology, which looks to solve exactly this issue. It's the mooring point which is the crucial piece in the puzzle.
Speaking to Energy Monitor, João Neves, director of strategy and business development at X1 Wind, says of the project: “X1 Wind and other companies have been working to take advantage of the floating environment in order to redesign the traditional orientation system, making it passive and allowing the whole platform to ‘passively’ orientate with the wind (rather than just the turbine).”
The PivotBuoy project deployed a part-scale prototype (named X30), designed to withstand sea states in the Canary Islands with a return period of 20 years. It uses a single-point mooring system, around which the floating platform can rotate according to the wind to enable maximum energy generation.
“This means that the platform can align with the wind direction without needing an active yaw system,” explains Neves.
The design has been shown to be particularly effective in strong winds of speeds above 7.5m/s, and is said to have minimal maintenance requirements. Already, the platform has been tested by significant environmental challenges – on 27 December 2023, the prototype faced waves that reached almost 7m in height and wind speeds of 18m/s.
“Throughout the storm, the unit behaved well with motions and accelerations matching the predictions in simulation models,” says Neves. “This underscored the reliability and robustness of X1 Wind's technology and design when facing harsh environmental conditions.”
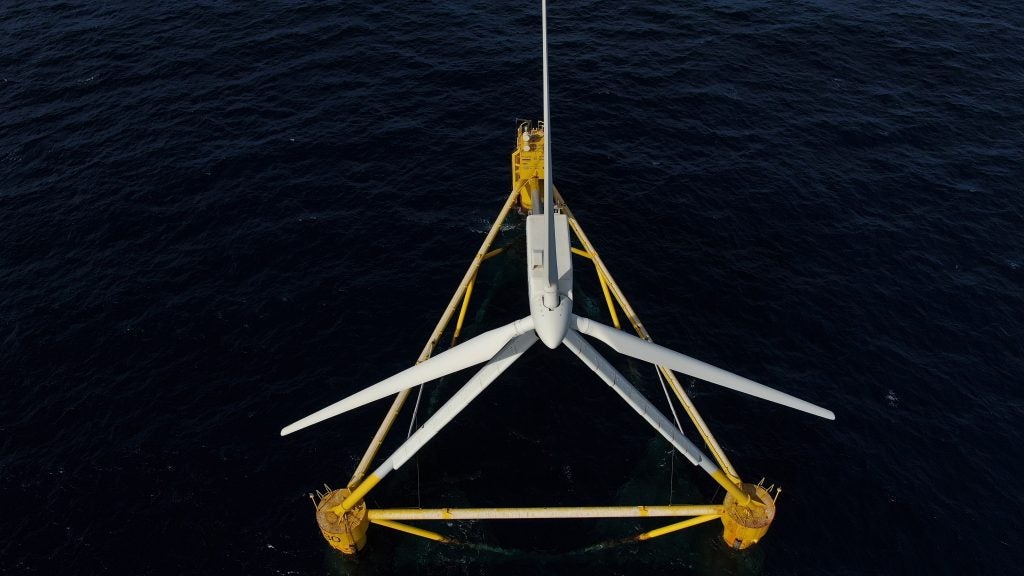
Commercialisation and its obstacles
Following its work on PivotBuoy, X1 Wind was selected by the European Commission to deliver the NextFloat project, which looks to scale up the solution with a view to deploying a 6MW prototype in the Mediterranean Sea. Engineering is currently underway, with construction expected to start in 2025, followed by the installation of the unit.
Considering the likely trajectory for the project, following on from the X30 prototype, Neves says: “The data obtained was very well-aligned with our simulation models and provided critical insights that are now being transferred to the NextFloat+ Project and commercial-scale ones, using standardised shapes, small diameters, and thin structural elements to enable mass production.”
Commercialisation will come eventually then, but the engineering considerations are multifaceted.
“Site selection is key, involving detailed wind resource assessment to ensure optimal energy production and understanding water depth and seafloor conditions for the mooring and anchoring systems,” explains Neves.
“Structural design must ensure platform stability and buoyancy to withstand varying sea conditions along with turbine integration considering load distribution and dynamic effects.”
There are some specific economic and regulatory obstacles too. Initial investments are expensive, and there is a need for new infrastructure to connect the turbines to the grid via subsea cable routing. Once building costs are overcome, there will still be expenses associated with maintaining the hard-to-reach infrastructure, which will require maintenance crews and robust monitoring and control systems.
Regulations around marine protection will also need to be considered in relation to widespread commercialisation.
Neves explains: “Environmental impact assessments are essential, focusing on protecting marine ecosystems, minimising noise and emissions during all project phases, and ensuring regulatory compliance. For example, in our case, besides the minimal seabed footprint, the NextFloat Project will present the installation of a bio-boosting system applied on the floater, which will boost the marine ecosystem around the platform.”