
Houses, skyscrapers, dams, bridges – every variety of building and infrastructure – all rely on cement. This, however, poses a problem for the environment: cement is responsible for 8% of global carbon emissions – or more than three times the emissions produced by aviation – and there is no easy way to get rid of them.
Cement is known as one of the ‘hard-to-abate’ sectors. But abate it must if the world is to stand a chance of limiting global warming to a manageable level. Worryingly, due to the industry’s long-lasting assets, 2050 is just one investment cycle away – so solutions need to be put in place today for the industry to hit net-zero emissions by mid-century.
Hot on the heels of the World Cement Association’s annual conference in Nanjing, China, earlier this summer, Energy Monitor caught up with WCA’s CEO, Ian Riley, to find out how the industry’s decarbonisation agenda is progressing.
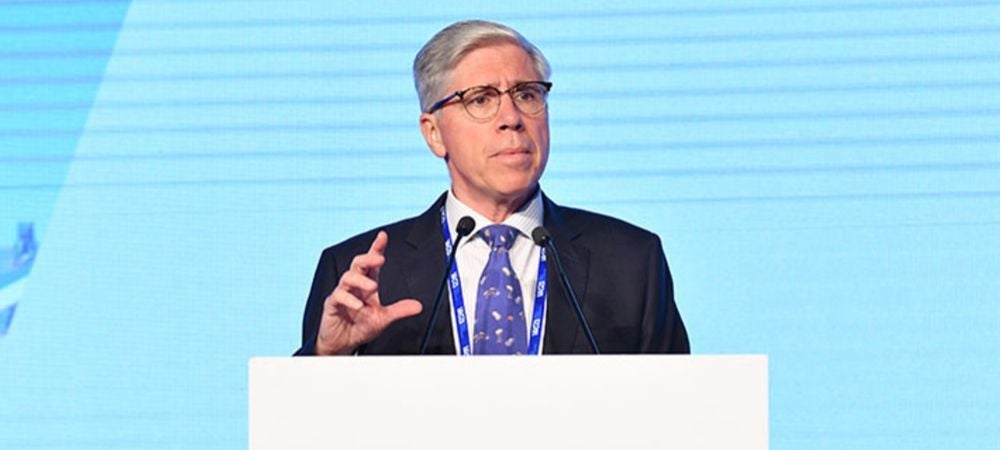
What progress has the cement industry made in its net-zero agenda lately?
Direct scope 1 emissions represent 90% of cement emissions – about two-thirds of which are coming from the limestone and a third from the energy. And there are three leavers the industry has pulled for 20/30 years now: energy efficiency, fuel switching to primarily waste-based fuels and reducing the clinker factor of the cement.
These levers have achieved a roughly 50% reduction in emissions in the last 30 years. And then there’s the one that we are extremely reluctant to move to, because it’s so expensive, but without which we don’t know how to get to net zero: carbon capture, use, and storage (CCUS). And CCUS projects have really taken off in the last year, at least in terms of project announcements – obviously, those that are actually operational is another story.
The issue is really economics. The cost of CCUS, for example, is completely prohibitive, unless everybody has to do it. So you have to have a regulatory framework which creates incentives for further decarbonisation. Obviously, we have that in Europe and to some extent in the US. The great thing with the EU is it’s really hard for them to change the rules, so you’ve got some consistency in policymaking.
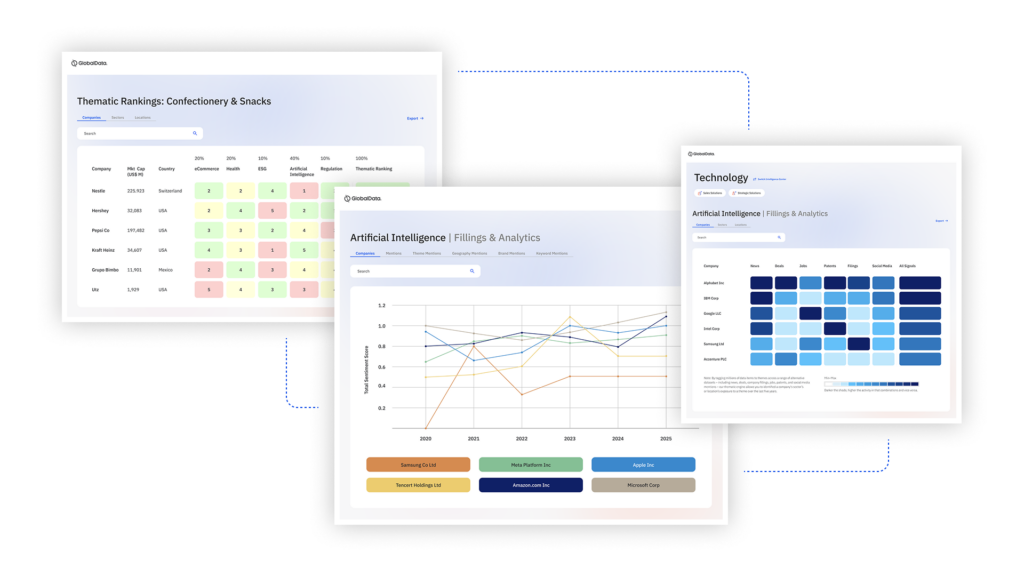
US Tariffs are shifting - will you react or anticipate?
Don’t let policy changes catch you off guard. Stay proactive with real-time data and expert analysis.
By GlobalDataIn the UK, the government last year decided to increase the amount of free allocations available, which is just the sort of thing that completely undermines the certainty you have on the long-term rules you’ll have to abide by. If you talk about investing significant amounts of money in decarbonisation, why would you do it in the UK when you can’t be sure that the rules aren’t going to change again. So it’s really not helpful.
There has been some progress in the last year. It’s very difficult to get figures that allow you to be terribly specific on this because most of the figures are published several years late so they don’t have a competitive impact. But I think you can see that there continues to be progress.
What developments have been made in tackling the industry’s process-related emissions?
There’s been an acceleration in the interest in calcined clays and LC3. In the very traditional OPC (Ordinary Portland Cement), you have 95% clinker. And of course, clinker is the part of cement that has the emissions. But you can reduce the clinker down to 50% with LC3 and have the same strength. The first plant to convert to LC3 was an Argos plant in Colombia, back in 2019, and a Portuguese cement company installed a brand new line in West Africa around the same time. But it went a bit quiet after that. But in the last year or so, we’ve seen a number of these announcements by Holcim and others in different parts of the world, which will lead to a substantial reduction in the carbon footprint and a reduction in the costs.
It’s a technology that makes sense in Europe with the carbon pricing, but in specific cases where there are other reasons it makes sense. For example, the reason that it worked in West Africa is there’s no limestone there; so all of the clinker is imported, which makes it very expensive. And if you can replace that with a local calcined clay, then it’s got lots of carbon and cost benefits. Clay is probably almost as widely available as limestone, so LC3 is something that can really scale.
What progress has there been in reducing the industry’s fossil fuel use?
Everywhere in the world, we’re seeing increased use of alternative fuels. That’s mainly waste-based fuels – some of that is biomass like wood chips and bamboo or from agricultural waste like rice husks, but, by and large, it’s fuels from municipal or industrial waste. You can burn anything in a cement plant, no matter how difficult it is to dispose of – so you’re doing something useful for society by getting rid of these oil sludges and things like that. So we do see more of that. But you have to have regulations surrounding waste in order to generate enough material for the cement plants to burn. Europe is already pretty big using alternative fuels, but in developing countries like China and India, there’s a lot of progress that’s been made over the last few years.
What can be done to reduce the vast projected demand growth for cement?
There’s a lot of nonsense talked about this. A lot of the forecasts you see suggest we’re going to see very large demand growth for cement between now and 2050. I just don’t think that’s right at all. People like the IEA and others haven’t understood how cement gets used. If we go back to 2020, China represented 57% of global demand, and that was really at the end of peak demand in China.
China hit a peak in about 2014 and then remained roughly flat between 2014 and 2021, and then has started to decline, and will continue to decline until its consumption is probably half of its peak demand. And we’ve seen the same pattern in many other countries; Japan, Korea, Taiwan. You can look at cement demand as a function of the economy. Once you get to a certain level, to some degree, you’ve already done it – you generally only build things once, so once it’s already built, you build less. So when you cut China’s 57% in half, that’s a big hole in overall demand in the market.
There are regions that are growing, and that will continue to grow, primarily Sub-Saharan Africa and India. But if you take those two together, they are a tiny fraction of the Chinese market: Sub-Saharan Africa has a consumption which is less than 100 kilos per capita, whereas China is 1600 kilos, and India is at about 350. The Indian market is quite large and will grow, so it gets close to the Chinese market. But even if the Indian market doubles, the Chinese market halving still leaves them short between the two of them – and the increase in Africa will only make up a small part of that. So, overall, we will see global demand declining over the next 20/30 years, not increasing.
Things like LC3 will also reduce the clinker factor in cement. Concrete demand is roughly flat, or declining slightly, but the clinker demand – the real emitter – is going to decline more quickly than that, because we’ll see greater use of other cementitious materials like calcined clay. And that’s really looking at it only from the cement perspective. If we look at it from the concrete perspective, there are other ways of making concrete that don’t use conventional cements. And as we get more carbon pricing, the cost of cement will increase and alternative concretes will become more attractive. Of course, a lot of them are outside the current standards but functionally they’re fine – the standards will adapt over time.
As countries require developers to reduce their embodied carbon per square metre of building, they will look for ways to do that, which will include using unconventional approaches to the less risky concrete applications. So we’ll also see a replacement of traditional concretes with novel concretes. Maybe also some replacement of concrete with timber – but there’s only a limited supply of timber, and there are limited things you can use it for. From the effects of concrete replacement and clinker replacement in cement, we’ll see a reduction in the emissions, even before we take into account CCUS or anything like that.
Cement is a highly localised market, so decarbonising it relies on compliance from a bewildering array of regional stakeholders, all with varying circumstances and priorities. What can be done about that?
The options for each country’s decarbonisation roadmap are reasonably well understood. It won’t be exactly the same solution everywhere but it really comes down to what’s the lowest cost way of getting there. And that depends on the regulations. So one of the important initiatives is CBAM (Carbon Border Adjustment Mechanism), which seeks to be a way of spreading the area of the globe that’s covered by carbon costs.
I suspect we’ll see carbon taxes spread by this sort of CBAM mechanism. Indeed countries like China, which have not even yet implemented a nationwide carbon ETS (Emissions Trading System) for the cement industry, are already thinking about CBAM and whether that plays a role there as well. There is some interest in whether CBAM might lead gradually to a bit more consistency in carbon pricing globally.
What’s the latest on the industry’s attempts to adopt CCS technology? I understand it’s been a very slow process. How close are we to getting commercial-scale projects?
We see a lot more carbon capture and storage (CCS) projects, in Europe and North America, but also in China. The largest operating CCS project in the cement industry is in China, and it’s a new “oxy-fuel” technology – there’s also a similar pilot facility being built in Europe, which will become operational next year. But in China, the first one was commissioned in March this year, and that’s a 200,000 ton/year capture facility, which is maybe a bit bigger than the Heidelberg plant in Brevik (Norway), which is about 150,000 ton/year.
Overall, there are over 100 that have been announced in the cement industry worldwide. But of course, these projects take a long time to execute. A lot of them are quite complicated, and we’re going to have an awful lot of bottlenecks to work through – on supply of critical equipment, the piping, etc. But nonetheless, there’s a lot of activity there, which will lead to progress over the next decade.
But if you look at the total amount that is being talked about, it’s still a very small portion of the cement capacity – even in Europe, it’s only around 10% total capacity. So it’s a start; but only a start. I think we’ll see within five or 10 years that most of the major cement producers are able to produce zero-carbon cement in at least one of their plants, but that’s still a long way from being a decarbonised industry.
We’re relying on the oil and gas companies for a part of the solution. You’ve got the cement plant generating the CO2, and then essentially a chemical plant, which is capturing the CO2, and then essentially an oil-and-gas system that’s taking it from there and storing it. So you’ve got a lot of different expertise that’s involved in this – that normally means that things don’t move that quickly. And that’s exactly what’s happened; CCS projects have taken a long time so far.
We don’t know how to decarbonise cement without CCS – we don’t have another alternative. There are lots of things we can do to reduce the carbon, but we can’t get down to zero today without CCS – maybe half if we were very optimistic. But, for the other half, we’re going to need CCS.
But CCS is so expensive. To put in CCS for a cement plant, you’re going to spend probably one and a half or two times the cost of your cement plant. The capital involved is enormous, and it only works if you’ve got the right financial incentives in place. In Europe, a combination of the carbon price and the expectation that that will increase as free allowances are removed, plus the capital subsidies that the EU is giving for the installation of CCS, is making it pretty easy for companies to commit to it; because they’re going to be competing with people who didn’t take advantage of that offer and had to pay all of their capital cost upfront, or had to pay the very high price that we expect to get to in 10 years time on the ETS.
Elsewhere, that’s not really started. If you go to China, India, Africa, the Middle East and so on, there isn’t anything in place that is going to give a return on these projects yet. And developed countries only make 10% of the total cement worldwide, and there’s not much happening in CCS in that 90% yet. So a lot of it does depend on continued progress in putting in place regulations that create incentives one way or another – through carbon pricing or subsidies or whatever – for cement companies to make these huge investments in CCS.
But it doesn’t make sense to put CCS on all of today’s cement plants. We already have a massive over-capacity anyway, so we don’t really need all the cement plants even today. And if demand is going to decline, we’ll need even fewer of them. And you certainly don’t want to put CCS on plants you don’t need. So somehow all of this has to be worked out over the next 20/30 years.
What role can governments play in helping to decarbonise the sector?
There are two roles that are really key with government. The first one is creating incentives. They can create incentives for the cement companies, they can also create incentives for the developers and the contractors. For example, in London now there’s a requirement to get new planning permission on large projects. You have to calculate the carbon footprint per square metre, and there’s a guideline on what’s an acceptable level – the aim is to reduce that by 40% by 2030 so that developers have an incentive to procure low-carbon materials.
Materials are the vast majority of their footprints. So it doesn’t have to be the government giving out money, but one way or another there has to be a financial benefit for doing the right thing: getting a subsidy, not paying a tax, not paying a cost, or whatever. That can be applied to the cement industry in the form of carbon pricing and emissions controls and so forth. It can be applied to the asset owners – the real estate developers or infrastructure companies – in the form of planning requirements on what new projects have to adhere to.
And then the second area is public procurement. The government is a big buyer of concrete worldwide: around half of concrete is procured by governments. So governments can make a big difference by insisting on using low-carbon materials on their infrastructure projects, which would help create markets for those materials. But they need to be willing to pay a premium on those projects.