Lithium-ion batteries are a key enabling technology of the energy transition. Scaled up versions of the batteries used to power mobile phones and laptops are now increasingly employed to power electric vehicles and to add flexibility to the electricity grid. If charged with low or zero-carbon electricity, lithium-ion batteries will dramatically reduce carbon pollution from vehicles and the power sector over the coming decades.
However, the convenience of this easily dispatchable, often portable power source comes at a cost for workers and the planet. The social and environmental toll of lithium-ion batteries has not been fully studied, especially in lithium-producing countries. This is the conclusion of a comprehensive review of research on lithium extraction led by Datu Buyung Agusdinata at Arizona State University’s School of Sustainability. If lithium-ion batteries are to be a sustainable part of the energy transition, policymakers will have to agree measures to reduce the water and carbon footprint of batteries, everything from mineral extraction, to their use in products, to recycling at the end of their life.
With growing demand for consumer electronics and EVs, the storage capacity of lithium-ion batteries installed in 2018 increased by nearly 800% over the previous ten years, finds Agusdinata and his co-authors. Lithium used in batteries jumped from 5,160 metric tonnes in 2007 to 19,780 metric tonnes in 2017. By 2030, 22,000 tonnes of lithium may be required just to meet the demand for EVs in the US.

With millions of EVs now being added to roads across the globe each year, the question of what to do about used batteries looms. Some EV battery packs will have a second life in stationary energy storage systems, but responsible management of the remainder will be a big challenge. By 2030, two million metric tonnes of used lithium-ion batteries could pile up around the globe each year.
More research will be needed to study the social and environmental impacts of such a massive expansion of the sector in such a short period.
“We suspect the full supply chain impacts have not been evaluated and the implications of the technology for sites distant from sites of consumption and manufacturing will be less understood than impacts closer to sites of consumption. The issue of lithium mining impacts on local communities needs to be urgently addressed,” conclude Agusdinata’s team.
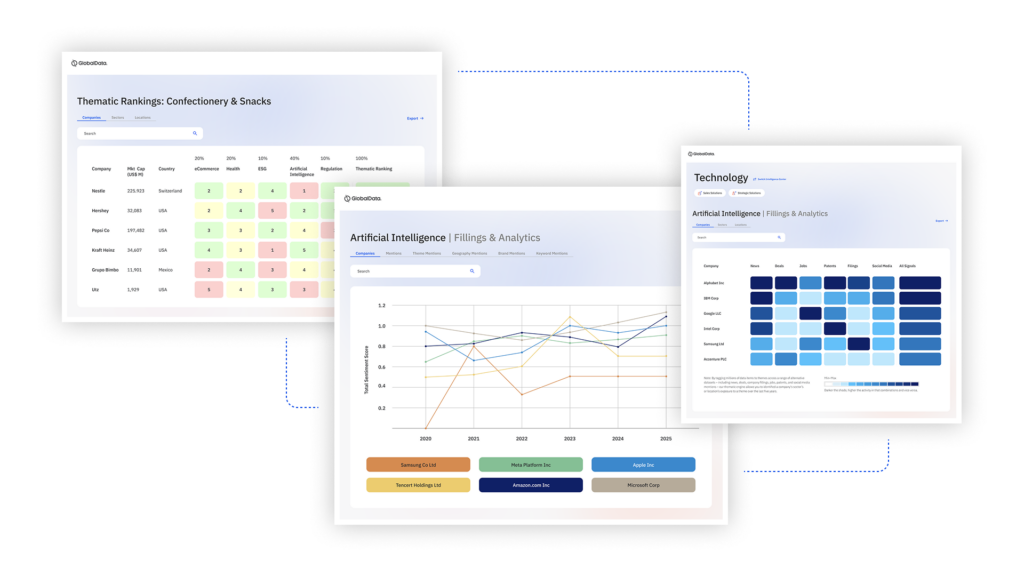
US Tariffs are shifting - will you react or anticipate?
Don’t let policy changes catch you off guard. Stay proactive with real-time data and expert analysis.
By GlobalDataGovernments also focused on scarcity
With countries jockeying to control a share of the global market for lithium-ion batteries, social and environmental concerns are forced to compete for the attention of policymakers with the national and economic security implications of scarce critical battery materials. Having fallen behind China in establishing a domestic lithium-ion battery supply chain, the EU and the US are racing to catch up.
The European Commission recently added lithium to its Critical Raw Materials list for the first time. To meet expected demand for EV batteries and energy storage systems, officials say Europe will need up to 18 times more lithium and five times more cobalt in 2030 than is currently used by the entire EU economy. The Commission plans to identify mining and processing projects for critical raw materials in Europe that can come online by 2025. In October 2020, the Commission launched the European Raw Materials Alliance.
In the US, several Cabinet-level federal agencies, including the Departments of Energy and Defense, launched the Federal Consortium for Advanced Batteries in September 2020 to coordinate work by agencies to establish a domestic supply of lithium batteries. The same month, President Donald Trump signed an executive order declaring the US’s dependence on “foreign adversaries” like China for minerals deemed critical to the country’s economic and military security a “national emergency”. Recommended executive actions to deal with the threat are to be included in a report due at the end of November 2020 and “may include the imposition of tariffs or quotas, [and] other import restrictions” on China and other countries.
California officials, meanwhile, are determined to develop a home-grown sustainable battery supply chain based on lithium recovered from brines brought to the surface as a byproduct of geothermal electricity generation. Geothermal lithium could also be a source of low-cost, domestic lithium for Europe, says Sanjeev Kumar from the European Geothermal Energy Council. Kumar cites the former tin mining region of Cornwall in south-west England and the Rhine River region of France and Germany as promising areas to source geothermal lithium in Europe.
Social and environmental concerns
Among the reasons California officials are so bullish on lithium recovery from geothermal brines is the potential to significantly reduce the environmental footprint of lithium-ion battery production. In May 2020, the California Energy Commission awarded grants worth a total of $7.8m (€6.6m) to two companies working to commercialise lithium recovery processes.
“The processes these projects will demonstrate have a relatively small physical footprint on developed land (with a footprint significantly smaller than large open mining pits and evaporation ponds used for lithium extraction elsewhere), inherent low water intensity as a by-product of the geothermal operations, and minimal waste streams,” says the California Energy Commission.
In their review of the impacts of lithium extraction, Agusdinata and his co-authors cite a host of social and environmental pressures in Chile’s Atacama Desert, one of the world’s primary sources of lithium. The tally includes extensive groundwater use by the mining industry; mining sites overlapping with nature conservation areas; and water scarcity triggering forced migration from villages and ancestral settlements. The vast evaporation ponds used to harvest lithium from brines can expose the surrounding environment to lithium, and the sodium carbonate used can contaminate water supplies if improperly stored.
Researchers are also tracking the environmental and social impacts of other critical battery components such as the nickel and cobalt used in nickel-manganese-cobalt and nickel-cobalt-aluminium lithium-ion batteries. With demand growing for EVs and consumer electronics, global nickel demand is expected to nearly double by 2030.
Manufacturers, guided by their own sustainability targets, will increasingly demand that suppliers adhere to environmental, social and governance best practices.
“EV OEMs [original equipment manufacturers] are expected to increasingly demand clean nickel,” say analysts at McKinsey & Company. “As OEMs start to define requirements in relation to the raw materials they use – quality of the nickel, environmental impacts, social concerns and geographical issues – the size of the pie will suddenly start to diminish.”
The source of the raw nickel – such as deposits of sulphide or laterite – determines the scope of potential environmental impacts. Sulphide orebodies must be smelted, says the McKinsey team, a process which emits SO2-rich gases, and the refined product leached out using sulphuric or hydrochloric acid. Laterite deposits, which cover hectares and are often located in the tropics, must also be leached, in this case with sulphuric acid or ammonia. The resulting tailings can include heavy metals, and the high-pressure leaching process is a large electricity user.
More than two-thirds of the world’s cobalt is produced in the Democratic Republic of the Congo. A fifth of Congo’s cobalt comes from artisanal mines where, says Unicef, up to 40,000 children work in dangerous conditions. And acid mine drainage, resulting from the exposure of sulphur minerals to air and water, pollutes surface water.
Recycling and the circular economy
In response to social and environmental concerns, governments are under increasing pressure to require manufacturers to report data on battery materials. China already requires manufacturers to assign a unique ID to batteries produced in the country to track them from production to end-of-life recycling. In Europe, data sharing could be done via a ‘Battery Passport’. The World Economic Forum (WEF) and the Global Battery Alliance want such a tool to be fully operational by the end of 2022. The concept was supported in an energy storage resolution adopted by the European Parliament in July 2020.
“The European Commission aims to make product passports a reality, starting with battery passports,” says Tilmann Vahle, project lead in circular materials management with research firm SYSTEMIQ. “Various information on batteries would have to be recorded and kept and reported by manufacturers.”
New market entrants have emerged to help battery manufacturers track supply chain information. Vahle cites two London-based startups: Everledger, which has “conducted pilots on tracking battery information across product lifetimes”; and Circulor, which is “tracking material properties all the way from mine to finished battery”. One of Everledger’s pilots is a partnership with the automaker Ford, backed with funding from the US Department of Energy. This project will use the internet of things and blockchain technology to track the life cycle of lithium-ion batteries used in EVs and portable electronics.
Used EV batteries may find a second life providing grid services in stationary energy storage systems. “Whether a second-life application is viable and sensible can only be decided on a case-by-case manner,” says Vahle. In China, all large lithium-ion batteries must be tested for suitability for second-life applications while, in the EU, lawmakers are working to improve the economic case for second-life batteries by streamlining the installation process, he adds.
Ultimately, however, all batteries will have to be recycled at end of life to create a sustainable cradle-to-cradle system. Some progress is being made to close that loop.
Redwood Materials, a start-up launched by Tesla co-founder JB Straubel, says it will recycle more than one gigawatt-hour’s worth of battery scrap materials from Tesla’s Nevada Gigafactory in 2020 under a partnership struck with Panasonic last year. The material recovered so far is modest, enough to build batteries that can power around 10,000 Tesla electric cars as compared with the half-million EVs expected to be assembled at the facility this year.
SYSTEMIQ’s Vahle says materials companies, including incumbents like Umicore, have made major improvements in recent years to enable high recovery rates for battery metals in their plants. German lithium-ion battery recycler Duesenfeld is scaling novel recycling processes capable of recovering more than 95% of all metals in batteries at a carbon intensity that is 40% lower than benchmark recycling processes, he adds.
“Even more radical approaches are being researched,” he says, “including bio-based recycling where microorganisms leach out metals with minimal energy inputs.”
[Keep up with Energy Monitor: Subscribe to our weekly newsletter]
The combined effect of circular economy and technology improvements that boost battery productivity, such as smart and bi-directional EV charging and ride-pooling, could reduce EV battery pack costs from $90 per kilowatt-hour (kWh) to $70/kWh, and slash an EV’s life cycle greenhouse gas emissions by around 50% compared with an internal combustion vehicle, by 2030, concludes a 2019 WEF and Global Battery Alliance report.
Industry front runners are leading public commitments to adopt more responsible practices.
In January 2020, WEF and the Global Battery Alliance announced that 42 global organisations, including automotive, mining, chemicals and energy businesses, had agreed to ten guiding principles for a sustainable battery value chain. The principles include commitments to ensuring the circular recovery of battery materials as well as pledges to eliminate child and forced labour and support responsible trade and anti-corruption practices.
The International Council on Mining and Metals also recently established a set of Mining Principles – environmental, social, and governance requirements agreed to by members, including sector giants such as Alcoa, BHP and Rio Tinto. Members are expected to conduct engagement with local stakeholders, avoid involuntary resettlement of families or communities, respect the rights of workers, and provide fair pay and working hours, among other measures.
As demand for EVs, and batteries more generally, grows globally, suppliers and manufacturers will be under increasing pressure to deliver on consumer expectations for more sustainable battery supply chains.